п; по абсолютному содержанию в жидком стекле М20 и Si02 в масс. %; по содержанию примесных оксидов АЬОз, Fe203, CaO, MgO, S03 и др
Группа жидких стекол - щелочных силикатных растворов весьма обширна. Входящие в эту группу силикатные системы классифицируют по следующим признакам: по степени полимерности кремнезема (числу атомов кремния) , по химическому составу, по содержанию воды и по виду катиона жидкие стекла подразделяют на калиевые, натриевые, литиевые и силикаты органических оснований (наиболее распространены силикаты четвертичного аммония).
Таким образом, щелочные силикатные системы-жидкие стекла представлены широким диапазоном составов, характеризующихся разной щелочностью, различной природой катионов (включая органические), различным составом силикат-анионов от мономерных до высокополимерных, присутствием в системе коллоидного кремнезема различных форм, различным агрегатным состоянием связок от жидкостей до порошков.
Практическое использование жидких стекол осуществляется по одному и трех направлений. Первое направление связано с проявлением жидких стеклоолвяжущих свойств - способности к самопроизвольному отвердеванию (образованием искусственного силикатного камня). Уникальной способностью жидкого стекла являются также его высокие адгезионные свойства і подложкам различной химической природы. В этих случаях жидкое стекло выступает в качестве химической связки для склеивания различных материалов, изготовления покрытий и производства композиционных материалов широкого назначения.
Второе направление предусматривает применение жидких стекол в качестве источника растворимого кремнезема, т. е. исходного сырьевого компонента для синтеза различных кремнеземсодержащих веществ - силикагеля, белой сажи, цеолитов, катализаторов, золя кремнезема и др.
Третья область относится к применению силикатов щелочных металлов в качестве химических компонентов в составе различных веществ. Это направление предусматривает использование жидкого стекла в синтетических моющих средствах, для отбелки и окраски тканей, при производстве бумаги.(9)
1.2.2. Характеристика промышленных жидких стекол.
Жидкие стекла, выпускаемые промышленностью, представляют собой густые вязкие прозрачные жидкости без видимых механических включений и примесей. Жидкое стекло может быть бесцветным, однако в большинстве случаев оно окрашено примесями в слабо-желтый или серый цвет. Содово- сульфатное жидкое стекло окрашено в более темные тона, связанные с влиянием остаточных количеств углеродного восстановителя в составе силикат-глыбы. В ряде случаев наблюдается легкая опалесценция растворов жидких стекол, вызываемая появлением в них полимерных разновидностей кремнезема.
Химический состав промышленного жидкого стекла определяется в основном составом исходных стекловидных щелочных силикатов, однако его примесный состав может формироваться также в ходе его производства (измельчение силикат-глыбы, автоклавное растворение, транспортирование, хранение).
Химическая характеристика промышленных жидких стекол в соответствии с действующей технической документацией включает содержание основных оксидов (Si02, R2O), их мольное соотношение (модуль), содержание примесных оксидов (АЬОз, Fe203, CaO, MgO, SO3) и плотность раствора. Содержание основных оксидов в промышленных натриевых жидких стеклах в пределах стандартной плотности приведено в табл. 5:
Таблица 5. Содержание Si02 и R20 в промышленных жидких стеклах.
Характеристика стекла
| Содержание оксидов. %
| Модуль п
| Si02
| Na20
| Низкомодульное (марка А)
| 29.7-30,7
| 12,3-13,2
| 2,31-2,6
| Среднемодульное(марка Б)
| 30.8-31,9
| 11,0-12,1
| 2,61-3,0
| Высокомодульное (марка В)
| 32,0-33,1
| 9,8-11,0
| 3,01-3,5
|
Силикатный (кремнеземистый) модуль жидкого стекла определяется по формуле n = Si02/R20 • m, где m - отношение молекулярной массы щелочного оксида к молекулярной массе Si02: mNa =1,032; mK =1,568; Si02, R20 - содержание оксидов, %.
Содержание примесей в жидком стекле, получаемом растворением содовой силикат-глыбы, не превышает, масс. %: полуторных оксидов (Аl2Оз + Fe203) - 0,25; СаО - 0,20; SO3- 0,15. Для жидкого стекла из содово-сульфатной силикат- глыбы эти нормы более высокие и составляют, масс. %: (Аl2Оз + Fe203)-0.40; СаО - 0,25; S03 - 1. Такие ограничения удовлетворяют требованиям большинства потребителей. При более высоких требованиях по содержанию примесных компонентов (например, для производства синтетических моющих средств, катализаторов, сорбентов) жидкое стекло получают растворением специальной силикат-глыбы более жестко нормированного состава (по ГОСТ 13079-81). Еще более чистые по содержанию примесных компонентов разновидности жидких стекол, требуемые для специальных целей, могут быть получены не из промышленной силикат-глыбы, а путем прямого растворения особо чистого кремнезема в едких щелочах.
Промышленное жидкое стекло выпускается в виде растворов высокой
плотности: натриевое -1,36-1,45 г/см1 и калиевое - 1,4-1,56 г/см . Для некоторых потребителей выпускаются еще более концентрированные натрий- силикатные растворы с плотностью 1,47-1,52 г/см" (для литейного производства и производства сварочных материалов).
Плотность жидкого стекла неоднозначно определяется концентрацией растворенного силиката щелочного металла, поскольку такой силикат может характеризоваться разным соотношением Si02 и Na20 (силикатным модулем).
1.2.3. Области применения жидкого стекла.
Как уже отмечалось выше, силикаты натрия и калия и их водные растворы (жидкие стекла) применяют по трем главным направлениям. Первое направление связано с проявлением жидким стеклом вяжущих свойств, обусловливающих его использование в качестве связующего в составе композиционных материалов (рис. 1). Жидкие стекла применяются в качестве компонента цементов - гетерогенных систем, включающих наряду с растворами силикатов тонкодисперсные порошки. Порошки образуют с жидкими стеклами химически взаимодействующую композицию (цемент). В таких цементах жидкое стекло является жидкостью затворения порошковой части. Жидкие стекла используют также в качестве неорганического клея (связки-адгезнва) - гомогенной системы, отвердевающей и проявляющей адгезионные свойства при ее обезвоживании и при взаимодействии с отвердителями (силикатизаторами), находящимися в твердом, жидком или газообразном состоянии. В последнем случае мы имеем дело с «отверждаемой связкой». В качестве «связки» или «отверждаемой связки» водорастворимые силикаты применяют как для изготовления композиционных материалов и покрытий, так и для склеивания (сборки) деталей и узлов агрегатов различного назначения. Рядом авторов установлено, что вяжущие свойства выше у натриевых жидких стекол, чем у калиевых
.Рис. 1. Области применения водорастворимых силикатов в качестве связующего.
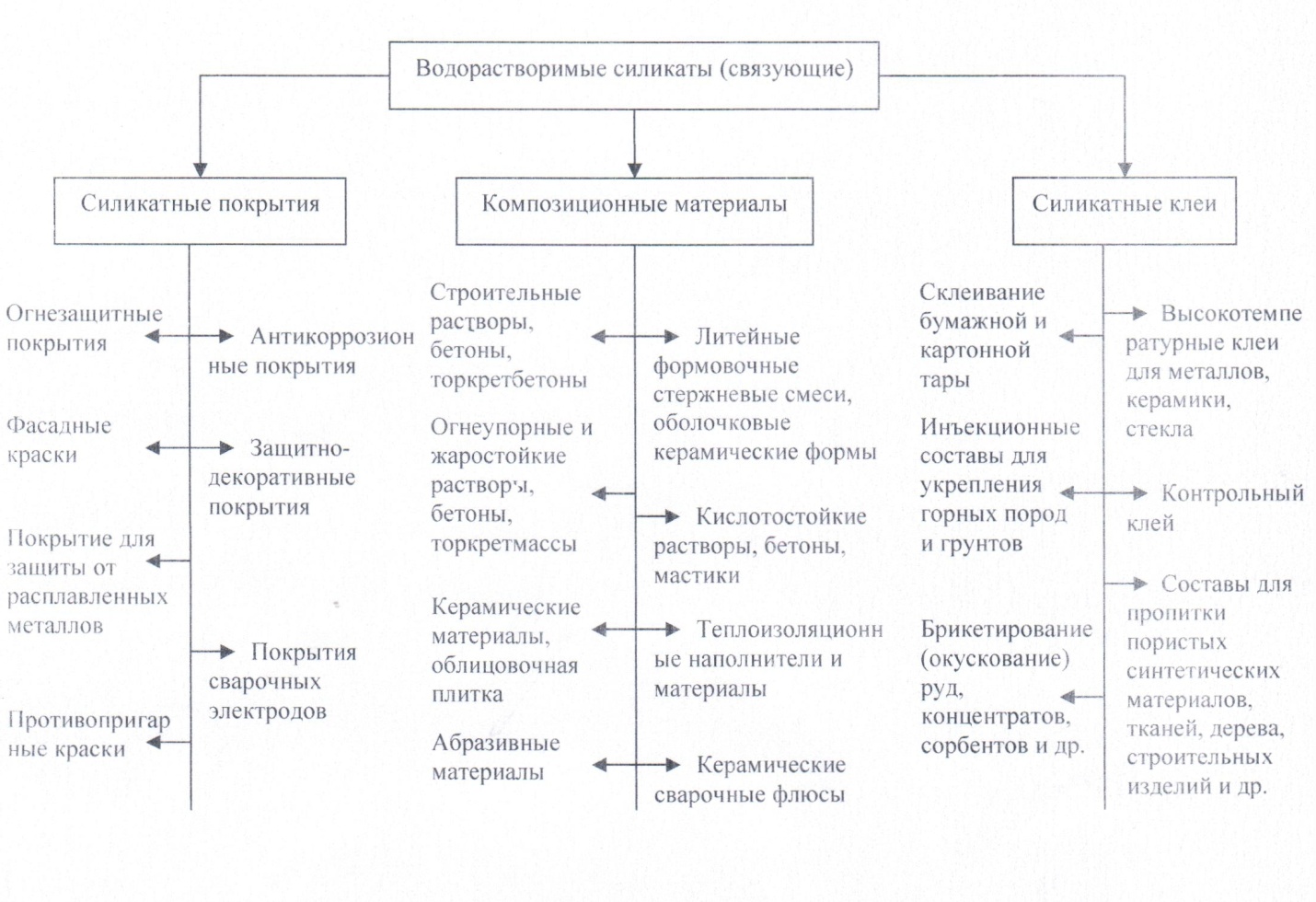 Наиболее крупным потребителем жидкого стекла является машиностроительное производство. В машиностроении жидкое стекло применяют в качестве связующего для изготовления форм и стержней, в основном при литье черных металлов в разовые песчаные формы.
Вторым крупным потребителем растворимого стекла является целлюлозно - бумажная промышленность, где жидкое стекло применяют для пропитки бумажной массы, а также в качестве клея для тарного картона и гофрокоробов.
Следующая большая группа потребителей растворимого стекла относится к химической и нефтехимической промышленности - это выпуск исходного компонента для производства катализаторов крекинга нефти, белой сажи, цеолитов, золя кремнекислоты, силикагеля, синтетических моющих средств.
Традиционным потребителем жидкого стекла является лакокрасочная промышленность, где жидкое стекло выступает в качестве пленкообразователя в составе силикатных красок (типа фасадных), антикоррозионных грунтов (цинкнаполненных), обеспечивающих протекторный механизм защиты металла, негорючих красок и др.
Важной областью использования жидкого стекла является строительная индустрия, где жидкое стекло применяют для производства бетонных конструкций и изделий.
В обзоре [14] сообщается об использовании растворимых силикатов для получения противопожарного стекла. Такое стекло состоит из многих слоев обычного оконного стекла, проклеенных жидким стеклом.
Применяют жидкое стекло также в огнеупорной промышленности для производства жаростойких и огнеупорных бетонов, в составе растворов для огнеупорной кладки, торкретмасс.
Эффективно жидкое стекло в производстве кислотоупорных бетонов и растворов, а также кислотоупорных замазок для кладки штучной кислотоупорной керамики.
Полные обзоры областей практического использования жидких стекол, сделанные в начале 50-х гг. Вейлом [15] и Григорьевым и Матвеевым [12], не потеряли своего значения до настоящего времени, современные сведения по этому вопросу содержатся в [13, 14]. 2. Экспериментальная часть.
2.1 Подготовка ЦСП.
Породу дробили и просеивали, собирая фракции с размерами частиц 0,102- 0,5 мм и 0,5-1 мм. В некоторых случаях после просеивания частицы ЦСП подвергали предварительному обжигу при 400С в течение 1 часа (для повышения водостойкости). 2.2 Получение образцов для выявления оптимальных условий. В качестве связующего применяли натриевое Жидкое стекло (ООО «Стройстекло», г. Скопин, Рязанская область, ГОСТ 13078-81) с плотностью 1,54 г/см3. Для получения шихт взвешивали определенные массы подготовленной ЦСП и смешивали полученные навески с рассчитанным объемом ЖС в различных соотношениях жидкой (Ужс> мл) и твердой (тЦСп, г) фаз. Во избежание неполного и неравномерного смачивания частиц твердой фазы жидкой и для создания влажности, удобной для формования образцов, в шихту в ряде случаев дополнительно прибавляли некоторый объем воды. Полученные смеси помещали в формы, в качестве которых использовали фарфоровые тигли, и оставляли при комнатной температуре в течение суток для частичного высушивания. Затем образцы подвергали обжигу в лабораторной печи (ТИП CHOJI-1,6.2,5.1/9-И5) при различных температурах. До и после обжига полученные смеси смешивали, определяя потери массы при прокаливании.
2.3Получение плитовидных образцов. Для получения плитовидных образцов взвешивали определенные массы (10-200 г) подготовленной ЦСП и смешивали полученные навески с рассчитанным объемом жидкого стекла в различных соотношениях жидкой и твердой фаз. Затем, действовали согласно методике 3. 2, но только смеси помещали в стальные формы. Образцы подвергали обжигу в лабораторной печи при оптимальной температуре 800 °С. 2.4Дополнительные условия получения образцов. В ряде случаев при получении образцов в форме плиток использовали сетку из стальной проволоки с размерами ячеек 1-2 см и толщиной 0,5-1 мм, для этого в стальную форму закладывали слоем около половины шихты, полученной в пункте 3.3, затем располагали сетку и уплотняли ее с помощью второй половины смеси, при этом сетка оказывалась в середине образца, полностью скрытая слоем шихты. Далее подвергали шихту обжигу при температуре равной 800 °С. При получении таких образцов стальную форму перед укладкой в нее образца натирали порошком графита. В других случаях вместо графита использовали несколько слоев целлюлозной бумаги, располагаемой между формой и образцом.
3. Результаты исследований
3.1. Поиск оптимальных условий.
Для нахождения оптимальных условий использовали два параметра: состав шихты и температура обжига. Для этого готовили образцы с массой 2,4 - 3,0 г различных составов. Показано, что при соотношении Vжс/mцсп от 2 : 1 до 1 : 2 наблюдали достаточное смачивание твердой фазы жидкой. При большем же количестве ЦСП в образцах смачивание было неполное, поэтому для создания нужной консистенции к шихте дополнительно добавляли определенное количество воды.
При выборе руководствовались следующими критериями:
а) Высокая пористость получаемых образцов;
б) Способность к самоформованию;
в) Достаточная механическая прочность;
г) Невысокий расход связующего;
д) По возможности, меньшая температура обжига.
Для выявления оптимальных температурных интервалов обжига образцов и их составов пользовались следующей схемой ( таблица 1 в проложении)
Определено, что наиболее оптимальным составом шихты является соотношение Vжс/mцсп равное 1 : 3, а температура - в интервале 700 - 800 °С. В таблице этим условиям соответствуют наиболее светлые поля. При этих условиях вышеуказанные критерии выбора сочетаются наилучшим образом. Получаемые таким образом образцы самоформуются, имеют достаточную механическую прочность и увеличиваются в объеме по сравнению с объемом шихты перед обжигом. При получении шихты оптимального состава нами рекомендовано дополнительно вводить в нее воду в объеме 50 - 80 % от объема ЖС. Важным параметром являются потери массы при прокаливании образцов, поэтому до и после обжига полученные смеси взвешивали и заносили в таблицы (см. приложение таблицы 2,3,4).
Видно, что потери массы происходят за счет улетучивания воды, специально добавляемой в шихту, воды содержащейся в ЖС и в исходной ЦСП.
3.2. Получение плитовидных образцов.
Ввиду того, что промышленная теплоизоляционная панель должна иметь размеры около 1 х 1 м при толщине 3-5 см, получали образцы большей массы размерами 15 х 15 см с толщиной 1 - 2 см для последующего измерения их механических свойств, удельного объема пустот и теплопроводности. После обжига шихты в стальных формах указанных размеров при резком охлаждении образцов наблюдалось их растрескивание с частичным разрушением. Во избежание подобных нежелательных процессов температуру в печи следовало снижать плавно (в случае лабораторной печи мы рекомендовали не извлекать из нее образцы до полного остывания).
Исходная ЦСП не отличается высокой водостойкостью, поэтому при приготовлении шихты происходило частичное разрушение гранул породы. Во избежание этого в ряде случаев повышали водостойкость ЦСП с помощью предварительного ее обжига при 400 °С. На основе полученного таким образом материала шихта четко сохраняла исходную зернистость, что проявлялось и после обжига при оптимальных условиях. Механическая прочность таких образцов оказалась несколько ниже, чем у аналогичных, полученных на основе ЦСП без предварительного обжига, в которых разрушившиеся при создании шихты частицы твердой фазы сплавлялись со связующим, образуя при этом с сохранившимися гранулами более сплошную массу. Еще одним существенным отличием образцов на основе предварительно обожженной и исходной ЦСП явилось уменьшение объема по сравнению с объемом исходной шихты в первом случае, и увеличение во втором. При этом следует отметить, что исходный насыпной объем шихты на основе обожженной ЦСП при равной массе превосходил объем шихты на исходной породе примерно в два раза.
Таким образом, в настоящей работе найден оптимальный состав и температурный интервал обжига для получения негорючих материалов с высокой пустотностью на основе природной цеолитсодержащей породы и связующего - жидкого стекла. Полученные в работе результаты перспективны при разработке технологии экологически чистых теплоизоляционных материалов на основе местного дешевого сырья.
3.3. Создание утеплителя на основе природной ЦСП.
Утеплители различных марок обладают стабильными теплотехническими показателями, и давно используются в строительстве и производстве взамен традиционных материалов (кирпич, бетон, дерево) благодаря своей низкой себестоимости и технологичности.
Ниже приведены сравнительные показатели использования различных материалов, для достижения одинакового результата. Сравнение различных материалов для одинаковой теплоизоляции.
Пеноплекс, 20 мм
Пенопласт, 30 мм
Минеральные утеплители, 38 Дерево, 250 мм
Ячеистый бетон, 270 мм Кирпичная кладка, 370 мм
Поэтому в настоящее время все более актуальной становится проблем рационального использования тепловой энергии и создании энергоэффективных домов. Вследствие чего возникает проблема создании более эффективных утеплителей, которые отличаются не только хорошими теплоизоляционными качествами, но и долговечностью, экологичностью. Эта проблема решается путем создания вакуумного наноструктурированного утеплителя, который получается в несколько стадий:
1) Создание наночастиц из ЦСП.
Получение определенной структуры.
Заключение полученной структуры в вакуумную пленку и создании вакуума.
В практических экспериментах получено 2 образца, характеристики которых представлены в следующей таблице ( см. приложение таблица 5).
Испытания проводились без оболочки и создания вакуума. После определения несущих способностей, в результате расчета определяем , что мы можем создать вакуум порядка 0,023 МПа для первого образца и 0,01 Мпа для второго. Данный эксперимент по этим наименованиям выполнялся в МГУ на строительном факультете.
Вакуум служит как дополнительное уменьшение теплопроводности, вследствие уменьшения концентрации материальных частиц, способных переносить тепло.
Данный утеплитель входит в состав «теплоизоляционной панели», которая сочетает в себе свойства декоративной отделки фасадов и лучшей теплоизоляции. Ожидаемая теплопроводность на порядок больше, чем теплопроводность современных утеплителей. Теоретическая теплопроводность 0,004 кВт/м2. Вакуумированный наноструктурированный утеплитель относится к группе негорючих, благодаря этому исключена возможность возгорания.
В наших климатических условиях существенную часть на эксплуатацтю зданий составляют расходы на отопление. Поэтому высокие теплоизоляционные свойства данного утеплителя из вакуумированной ЦСП делает ее чрезвычайно экономичным строительным изделием. А долгий период эксплуатации, экологичность, высокая стойкость к биологическому воздействию, отсутствие водопоглощения, небольшой вес, отсутствие ограничений по применению делают ее очень выгодной.
3.4. Дополнительные условия получения механически прочных образцов.
При внедрении полученных результатов в промышленное производство очень важно выбрать долговечную форму с отсутствием прилипания к ней полученных теплоизоляционных плит. Наиболее оптимальными будут стальные формы без боковых стенок , на которые формовочная машина будет укладывать шихту требуемой формы. Чтобы избежать окалинообразования рекомендуется заменить стальные подложки на керамические плиты. Весьма нежелательным процессом при получении таких плит является прилипание шихты к подложке при обжиге. Во избежание этого мы рекомендуем перед укладкой шихты на подложку наносить тонкий слой порошка графита, другим выходом из этой ситуации является замена графита на древесные опилки, которые в большом количестве получают как побочный продукт деревообрабатывающей промышленности и является весьма доступным материалом. В нашей работе мы успешно применили в качестве такой подложке целлюлозную бумагу. Это резко снизило прилипаемость образца к подложке. При получении плит промышленных размеров (120см х 90см х 3см) возникает проблема сохранения целостности получаемых форм.
В случае разработки материалов избежание растрескивания - очень важная проблема. Для ее решения мы предлагаем при формовании плит использовать стальную проволочную сетку с размером ячеек 2 - 3 см и диаметров проволоки 0,5 - 1 мм. Проволока располагается в толще образца почти по всему контуру формы, одним слоем посередине толщины образца. Применение нами такой сетки положительно решило проблему сохранения целостности образцов после обжига.
Заключение.
Разработана методика получения пористых материалов с высокой пустотностью на основе местной цеолитсодержащей породы и жидкого стекла.
Найдены оптимальный состав и температурный интервал обжига и прочие условия для получения экологически чистых негорючих материалов на основе местного дешевого сырья.
Выявлены физико-механические характеристики (плотность, пористость, прочность на изгиб, прочность на сжатие) полученных образцов, имеющих форму плит.
Рекомендовано, при получении теплоизоляционных плит промышленного размера, внедрение в образцы металлической сетки для увеличения механической прочности.
Для уменьшения адгезии разработанных плит с формой для их обжига предложено использование доступного материала - древесных опилок.
Список использованных источников.
Брек.Д. Цеолитовые молекулярные сита/Д.Брек.-М.:Химия, 1976. -780с.
Сендеров Э.Э. Цеолиты. Их синтез и условие образования в природе/Э.Э.Сендеров, Н.И.Хитаров-М.:Наука., 2000. - 281 с.
Жданов С.П. Химия цеолитов/ С.П.Жданов, Е.Н.Егорова.-Л.:Наука 1998-158с.
Челищев Н.Ф. Цеолит - новый тип минерального сырья/Н.Ф.Целищев, Б.Г Беренштейн, В.Ф. Володин.- М.:Недра. 1999. - 176с.
Цеолитсодержащие породы Татарстана и их применение/ под ред. А.В. Якимова, А.И.Бурова. Казань. : ФЭН, 2001. - 172с.
Природные цеолиты. Труды Советского-Болгарского симпозиума по исследованию физико-химических свойств природных цеолитов (Под ред. Ф.И.Броучек-Тбилиси.:Мецниереба.1979. - ЗЗЗс.
Крешков А.П. Природные цеолиты-М.:Химия1985. - 224с.
Челищев Н.Ф., Володин В.Ф. Крюков B.J1. Ионообменные свойства природных высококремнистых цеолитов. - М.:Наука 1988.
Корнеев В.И., Данилов В.В. Производство и применение растворимого стекла. Л.: Стройиздат, 1991. 176 с.
Григорьев. П. Н., Матвеев М. А. Растворимое стекло. М. :
Промстройиздат. М., 2000. - 444 с.
11 .Weldes Н. Н., Lange К. R. Ind. Eng. Chem. 1969. V. 61, N 4.
12. Friedeman W. //Glasstechn. Ber. 1985. 58, N 11. s. 315-319
Vail J. G. Soluble Silicates. New York. 1952. V. 1, 2.
|