|
Получение черных металлов.
В чистом виде железо почти не применяется и не встречается в природе, а применяется в виде сплава с углеродом и др. металлами.
К черным металлам относятся железоуглеродистые сплавы. Их разделяют на две группы – чугуны и стали.
Если в сплаве менее 2% углерода – сталь.
Если в сплаве более 2% углерода – чугун.
Наибольшее количество чугуна идет на получение стали.
Основным способом получения чугуна является доменный процесс.
Доменная печь работает непрерывно много лет до капитального ремонта.
Для выплавки чугуна нужны – железная руда, флюсы и топливо.
Железные руды представляют собой главным образом соединение железа с кислородом (окись железа) и пустой породы в виде песка, глины и известняка.
Флюсы – минеральные вещества, добавляемые в доменную печь для понижения температуры плавления пустых пород, удаления золы и серы, а также остатков сгоревшего топлива. Флюсы образуют с пустой породой и золой топлива легкоплавкие сплавы, которые отделяются от металла в виде шлака. В качестве флюсов применяют известняк, кремнезем, кварц и песчаник.
Топливом служит кокс и природный газ.
Цветные металлы.
1. Медь. Цвет – розовато-красный. Очень вязкий и мягкий металл. Хорошо поддается холодной и горячей обработке, но плохо льется. Темп. пл. 10830
Хорошо проводит теплоту и электричество.
Применяется в виде листов, лент, труб, прутков, проволоки.
2. Цинк. Цвет серовато-белый с синеватым оттенком. Блестит на изломе, но быстро темнеет на воздухе.
Строение цинка всегда кристаллическое.
При обычной температуре цинк хрупок. При температуре 100-1500 он делается ковким и тягучим и может быть прокатан в листы.
Выше 1500 ковкость опять исчезает, а при температуре 2500 его можно истолочь в порошок.
Температура плавления 4490.
При температуре 9000 цинк закипает и превращается в пар.
Цинк плохо обрабатывается напильником.
В горячем состоянии хорошо прилипает к железу и обладает антикоррозионной стойкостью (оцинкованное железо).
3. Алюминий. Цвет серебристо-белый. Добывается из глины электротехническим путем, поэтому относительно дорог.
Металл мягкий, вязкий. Легко отливается, прокатывается в проволоку, сваривается, штампуется.
Темп. плавл. – 6570.
4. Олово. Цвет серебристо белый. Металл мягкий, тяжелый, обладает хорошей ковкостью, имеет кристаллическое строение.
Темп. плавл. – 2320.
5. Свинец. Основное свойство свинца – большой удельный вес 11,4.
Самый мягкий из всех металлов.
Темп. плавл. – 3270. В чистом виде цветные металлы почти не используются, а используются в виде сплавов.
Сплав образуется почти исключительно в жидком состоянии. Особенность сплавов то, что их температура плавления почти всегда ниже температуры плавления чистого металла, входящего в сплав.
1. Бронза – сплав меди с оловом. Содержание олова от 0,5 до 30%. Чем больше олова в сплаве, тем он более твердый.
Цвет бронзы желтый. Бронза хорошо проводит электричество, мало окисляется на воздухе и от кислот.
Используют для изготовления вкладышей подшипников, водопроводных кранов, клапанов, корпусов насосов.
Темп. плавл. – 900-10000.
2. Латунь – сплав меди с цинком. Содержание цинка 10 – 40%.
Латунь хорошо сохраняет полировку, куется, штампуется и льется.
Темп. плавл. – 980-10500.
3. Баббиты – сплавы на основе олова, свинца и др. металлов. Обладают высокими антифрикционными свойствами и используют для изготовления вкладышей подшипников скольжения. Основные свойства металлов.
Приступая к изготовлению какого-либо изделия, необходимо правильно выбрать наиболее подходящий для него материал.
Правильный выбор можно сделать, зная свойства металла или сплава.
Различают механические и технологические свойства.
Механические свойства металлов – свойства, которые позволяют металлам сопротивляться внешним воздействиям.
К механическим свойствам относятся:
1. Прочность - способность металла или сплава воспринимать действующие нагрузки, не разрушаясь;
2. Твердость - свойство материала сопротивляться проникновению в него другого, более твердого материала;
3. Упругость - свойство металла или сплава восстанавливать первоначальную форму и размеры после снятия нагрузки, вызвавшей их изменение. (пружины)
4. Вязкость - свойство тел, пластически деформируясь, необратимо поглощать энергию внешних сил;
5. Пластичность - способность изменять форму под действием внешних сил, не разрушаясь и сохранять ее после того, как будет снято действие сил. (гибка, прокатка, штамповка).
6. Хрупкость – способность тела разрушаться под действием внешних сил практически без пластических деформаций. Технологические свойства металлов – свойства, которые определяют способность металлов обрабатываться с помощью различных технологических процессов.
К технологическим свойствам относятся:
1. ковкость - свойство металла или сплава получать новую форму под действием удара;
2. жидкотекучесть - свойство металла или сплава в расплавленном состоянии хорошо заполнять литейную форму и получать плотные отливки;
3. обрабатываемость резанием - свойство металла или сплава подвергаться обработке резанием различными инструментами;
4. свариваемость - свойство металлов соединяться в пластичном или расплавленном состоянии;
5. коррозийная стойкость - свойство металлов и сплавов противостоять коррозии. Зная свойства того или иного металла, из которого будет изготовлено какое-либо изделие, необходимо выбрать самый целесообразный способ его обработки.
Это может быть:
1. обработка металла резанием (на станках или вручную).
2. литье – заливка расплавленного металла в специальную литейную форму, в которой он, застыв, сохранит очертания данной формы.
3. пластическое деформирование – прокатка, волочение, ковка, штамповка, прессование.
4. метод порошковой металлургией – порошки различных металлов путем прессования и спекания получают новый материал и детали готовой формы.
5. электроэрозионная обработка – разрушение отдельных слоев металла под действием электрического разряда.
6. электрохимическая обработка – под действием электрического тока разрушается поверхность металла, помещенного в электролит. (гальваника)
7. ультразвуковой метод – под действием ультразвуковых колебаний энергия вибрирующего инструмента передается частицам абразивного порошка, который, находясь во взвешенном состоянии в воде или масле, производит разрушение обрабатываемого слоя поверхности заготовки. Этим способом обрабатывают твердые материалы (твердые спеченные сплавы, алмаз).
8. сварка – получение неразъемного соединения металлических деталей, путем их местного сплавления.
Сортовой прокат.
Для изготовления различных изделий и деталей в промышленности и строительстве используют различные по форме металлические профили.
Эти металлические профили получают прокаткой нагретого металлического слитка через прокатные станы.
Из программы пятого класса известно, что листовой металл и проволоку получают тоже прокаткой.
Сортовой металлический прокат – продукция прокатных станов в виде полуфабрикатов, подлежащих дальнейшей обработке для получения готовых изделий.
Основные профили сортового проката:
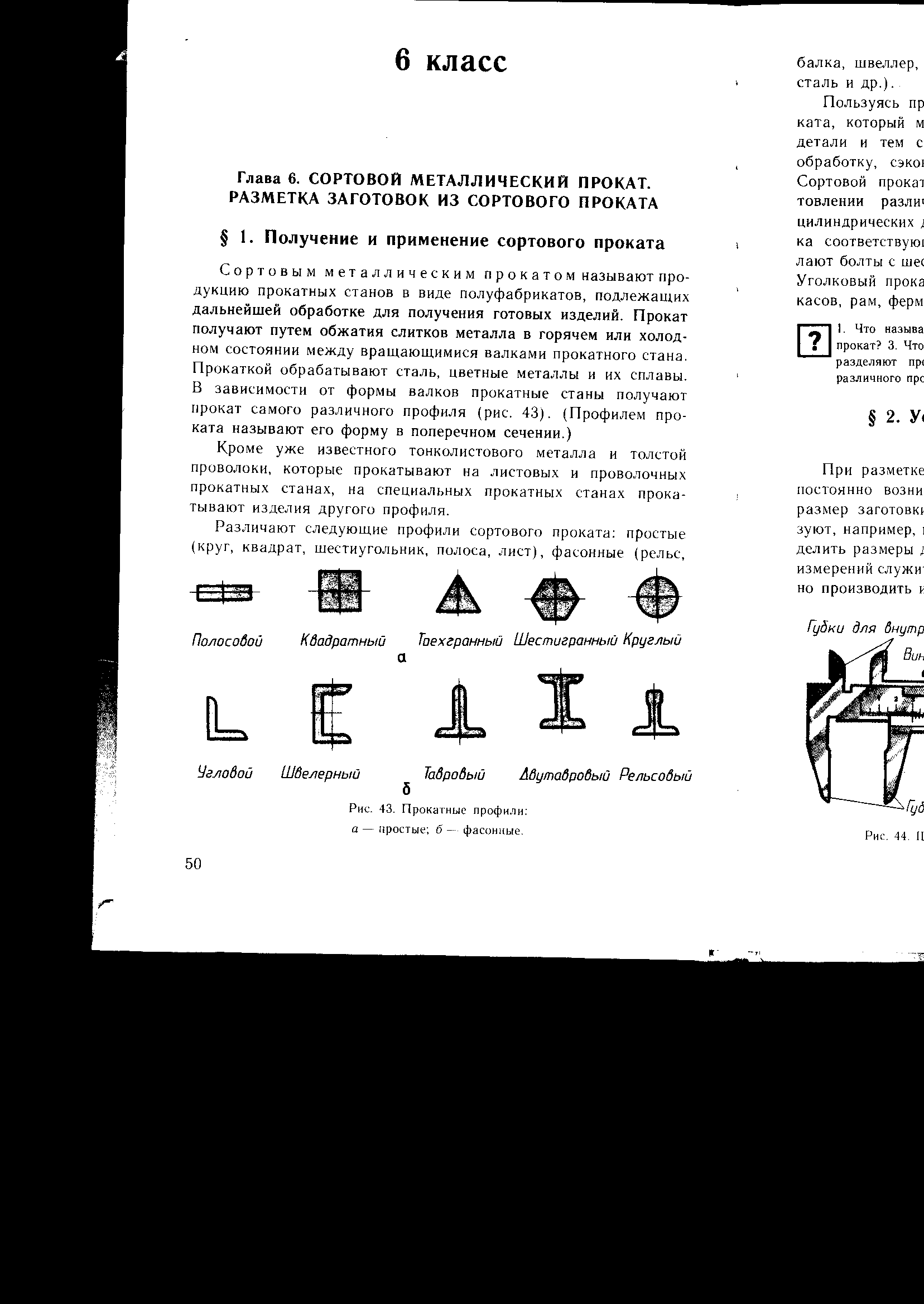
Сортовой прокат используют в качестве заготовок при изготовлении различных деталей. (болт, гайка из шестигранника). Практическая работа: ознакомление с видами сортового проката, металлами и их сплавами. Изучение свойств металлов.
Тема: Понятие о процессе резания металлов.
Цель урока: дать понятие о процессе и основных условиях обработки металлов резанием. Рассказать о шероховатости поверхности их обозначении на чертежах и способах контроля и получения в зависимости от способа обработки.
Оборудование: образцы заготовок с различной шероховатостью поверхности, заготовки, ножницы по металлу, напильники с различной насечкой, шлиф. шкурка различной зернистостью, токарный станок по металлу, полировальный станок, паста ГОИ, плакаты.
Содержание:
Одним из технологических свойств металлов является обрабатываемость резанием, т.е. способность металла поддаваться механической обработке режущими инструментами.
Обрабатываемость резанием зависит от твердости, вязкости и др. свойств металла.
Один и тот же металл имеет различную обрабатываемость при различных способах обработки.
Труднее обработать сталь с высоким содержанием углерода.
При обработке металлов резанием происходит изменение формы заготовки путем снятия стружки с применением металлорежущего инструмента и на металлорежущих станках.
Резка выполняется со снятием стружки (опиливание напильником, резание слесарной ножовкой, точение на станке, сверление отверстий) и без снятия стружки (резание ножницами, штамповка).
Как бы хорошо ни была обработана заготовка, при сильном увеличении на ее поверхности можно заметить следы режущих кромок инструментов, которыми она обрабатывалась. Эти следы образуют микронеровности в виде мелких впадин и гребешков.
Шероховатость - совокупность всех микронеровностей, образующих рельеф поверхности детали.
Шероховатость поверхности значительно влияет на качество детали. При низкой шероховатости деталь становится более гладкой и лучше сопротивляется износу, улучшается внешний вид детали. Но получение низкой шероховатости требует больших затрат труда. Однако низкая шероховатость может иметь и негативные моменты. Например, с очень гладких и испытывающих сильное давление трущихся поверхностей может выдавиться смазка. В результате молекулярного взаимодействия поверхности без смазки могут слипнуться, а это приведет к задирам, к сильному поверхностному износу деталей.
В зависимости от условий работы и других факторов поверхности деталей обрабатываются с различной степенью шероховатости.
Критериями шероховатости является высота неровностей по десяти точкам Rz и среднее арифметическое отклонение профиля Ra.
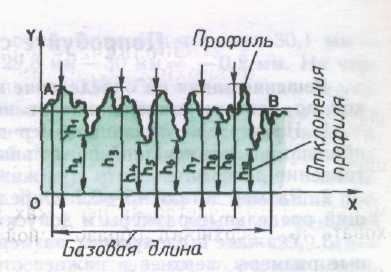
Стандарт устанавливает 13 классов шероховатости (1-13)
Размер шероховатости поверхности измеряется в микрометрах (мкм). Для контроля шероховатости используют эталоны шероховатости поверхностей, с которыми сравнивают обработанную поверхность, а в отдельных случаях — специальные приборы. Н а рабочих чертежах шероховатость обозначают для поверхностей, у которых она обусловлена требованиями конструкции.
- шероховатость поверхности метод, получения которой не
регламентируется.

 - шероховатость поверхности, образуемая снятием слоя
материала (точение, сверление, опиливание)

 - шероховатость поверхности которая должна быть получена без удаления слоя металла (литье, прокатка).
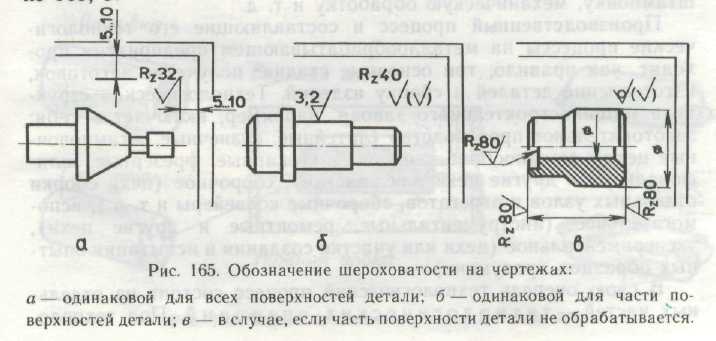 Малую шероховатость поверхности при обработке металла можно достичь путем окончательного опиливания поверхности металла напильником с мелкой насечкой, дальнейшей шлифовкой мелкозернистой шкуркой и полировкой на полировальном станке.

Практическая работа: Упражнения по доводке поверхности заготовки различными напильниками. Отделка изделия шлифованием и полированием. Контроль качества сравнением с эталоном. Тема: Разъемные и неразъемные соединения.
Цель урока: дать понятие о сборочном чертеже изделия, видах соединения деталей, взаимозаменяемости деталей и ее назначении в производстве и эксплуатации изделий.
Оборудование: сборочные чертежи изделий, образцы изделий с разъемными и неразъемными соединениями, заготовки (детали) для сборки, плакаты.
Содержание:
Чтобы изготовить изделие из нескольких деталей, сначала изготавливают каждую деталь по их чертежам, а затем собирают изделие.
Для сборки изделия из готовых деталей пользуются сборочными чертежами.
На сборочных чертежах изделие изображают в собранном виде. Размеры указывают только те, которые необходимы для сборки.
В правом нижнем углу располагают основную надпись, в которой указывают название изделия, масштаб и другие данные, относящиеся к изделию в целом.
К сборочному чертежу прилагают текстовый документ – спецификацию. В ней указывают порядковые номера (позиции) деталей, входящих в изделие, название каждой детали, количество деталей, входящих в изделие и материал из которого они изготовлены.
Около каждой детали на сборочном чертеже наносят номер позиции, присвоенный данной детали в спецификации. Многие изделия, выпускаемые промышленностью, состоят из нескольких сотен и даже тысяч деталей. Детали и узлы к одному изделию могут изготавливать десятки заводов. Такое массовое производство требует, чтобы каждая деталь при сборке изделия точно подходила к своему месту, без какой-либо дополнительной обработки или подгонки. В свою очередь при эксплуатации и ремонте изделий возникает потребность быстрой и несложной замены одной детали другой без дополнительной подгонки.
Указанным требованиям удовлетворяет принцип взаимозаменяемости.
Взаимозаменяемость – свойство независимо изготовленных по одному чертежу деталей, занимать свое место в сборочной единице без дополнительной механической или ручной обработки с обеспечением нормальной работы собираемого изделия.
Основное условие взаимозаменяемости – изготовление деталей с определенный точностью, в пределах заранее установленных допустимых отклонений от расчетных размеров и формы.
Точность – степень соответствия фактических размеров и формы деталей к расчетному, т.е. к размеру, указанному на чертеже.
К понятию точности, также относят качество обработки поверхности, характеризуемое шероховатостью.
Достичь абсолютной точности размеров практически невозможно. Причин этому много: неточность формы рабочей части инструментов, неточность в изготовлении приспособлений, нестабильность в режимах работы станков, погрешности измерений и т.д.
При изготовлении детали неизбежны отклонения (погрешности изготовления) геометрических параметров от номинальных значений (значений, указанных на чертеже).
Погрешности, при которых сохраняется работоспособность изделия, называются – допусками.
На рабочих чертежах, по которым ведется изготовление деталей, указываются номинальные — основные расчетные размеры.
Размеры, которые фактически получены при изготовлении детали, называют действительными размерами.
Для достижения необходимой точности изготовления детали нужно знать, в каких пределах допустимо отступление от номинального размера. Эти размеры называются предельными.
Различают наибольший предельный размер, больше которого изготовлять нельзя, и наименьший предельный размер, меньше которого изготавливать также нельзя.
Если от наибольшего предельного размера отнять номинальный размер, то получим величину, называемую верхним отклонением. При вычитании номинального размера из наименьшего предельного размера получают величину, называемую нижним отклонением. Для выполнения определенных функций в машине детали соединяются между собой, образуя подвижные и неподвижные соединения.
В подвижных соединениях одна из деталей может перемещаться относительно другой.
Неподвижные соединения образуют элементы конструкций из нескольких деталей, скрепленных между собой неподвижно.
В свою очередь соединения могут быть разъемные и неразъемные.
1. Неразъемные соединения не позволяют разобрать конструкцию без разрушения соединяемых и соединяющих деталей. (Заклепочные соединения, сварные соединения, соединения с помощью пайки и склеивания).
2.Разъемные соединения можно разбирать без разрушения деталей и соединяемых элементов.
К ним относят:
1. Резьбовые соединения – применяются в конструкциях, по условиям, работы которых требуется разборка и последующая сборка.
При соединении деталей одним болтом, винтом или шурупом, работа при сборке сводится к тому, чтобы достаточно сильно стянуть их, не допуская разрыва.
Болт имеет шайбу и гайку, размеры, которых согласуются с размерами болта.
Высота гайки делается равной диаметру болта.
Шайбы используют для предохранения металла изделия от смятия головкой болта или гайки.
Иногда для скрепления деталей используют шпильки – круглый стержень, имеющий с двух сторон резьбу. Один конец шпильки завинчивается до отказа в одну из соединяемых деталей, а другой конец проходит через вторую деталь и на него навинчивается гайка.
2. Шпоночное соединение состоит из шпонки, вала и ступицы и служит для передачи крутящего момента.
Шпонки бывают: призматические, сегментные, клиновые.
3. Шлицевые соединения служат для неподвижной установки деталей на валах.
Выступы на валу выполняют роль шпонок, а впадины на втулке роль шпонок.
Практическая работа: чтение сборочного чертежа, зачистка заусенце6в, подгонка деталей, сборка изделия. Сборка и разборка предложенных разъемных соединений.
Тема: Отделка изделий из металла.
Цель: ознакомить учащихся с вариантами и приемами отделки изделий из металла.
Оборудование и инструменты: шлифовальная шкурка, бархатные напильники, изделия или детали.
Содержание:
Отделка изделий из металла производится для придания красивого внешнего вида изделию, а также с целью предотвращения коррозии.
Окончательная обработка деталей из металла включает:
1. обработку поверхностей бархатными напильниками;
2.обработку поверхностей мелкозернистой шлифовальной шкуркой;
3. нанесение декоративных или антикоррозийных покрытий.
Металлические изделия покрывают красками, эмалями, тонким слоем металла и т.д.
Широко применяется покрытие поверхностей металлических изделий окисными пленками - оксидирование. При такой отделке изделие нагревается в муфельной печи и охлаждается в специальном растворе. Поверхность приобретает черный или темно-синий цвет и называется воронением. На предприятиях антикоррозийную отделку металлических изделий выполняют:
лудильщики - покрытие оловом;
гальваники - электролитическое покрытие (хромом, никелем);
металлизаторы (покрытие любым распыленным металлом). Рабочие данных специальностей должны хорошо знать свойства металлов и сплавов и устройство установок для отделки изделий.
Практическая работа: зачистка изделия бархатным напильником, нанесение на поверхность изделия соответствующего покрытия.
Тема: Лабораторно-практическая работа «Изготовление изделий из металла».
Цель: выявить уровень усвоения учащимися приемов обработки металлических заготовок при изготовлении различных деталей.
Оборудование и инструменты: слесарный верстак, набор слесарных инструментов, измерительный инструмент, заготовки различных изделий.
Ход урока
I. Вводная часть.
Расскажите о правилах безопасности при выполнении резки, рубки и опиливании металла.
Какие инструменты применяются при резке, рубке и опиливании металла?
Вспомните из программы 5 класса, какие инструменты используются при разметке.
Какие вы знаете измерительные инструменты?
II. Практическая часть.
• Учитель раздает заготовки изделий.
Это могут быть: угольник оконный; угольник для крепления столов; ручки к ящикам; лопатка детская; гаечные ключи; угольник слесарный и др., исходя из возможностей мастерской.
Далее учащимся необходимо:
1. выполнить эскиз детали;
2 .составить технологическую карту (определить последовательность операций);
3. выполнить разметку;
4. произвести рубку, резку, опиливание в зависимости от выбранной заготовки;
5. произвести контроль качества выполненной работы.
• Учитель постоянно обходит рабочие места и оказывает помощь в выполнении задания, исправляя допущенные в ходе выполнения задания ошибки.
III. Заключительная часть.
Учитель оценивает выполненную работу и подводит итоги усвоения учащимися приемов обработки металла. Отмечает лучшие работы. Провести уборку рабочих мест и мастерской.
7 класс.
Тема: Общность механизмов различных станков. Устройство токарно-винторезного станка.
Цель урока: изучить основные виды механических передач в механизмах станков. Ознакомиться с основными узлами токарно-винторезного станка и их назначением. По кинематической схеме ознакомиться со взаимодействием различных механизмов станка.
Оборудование и наглядные пособия: плакаты, макеты или рисунки механических передач, применяемых в токарном станке. Токарно-винторезный станок ТВ-6.
Содержание:
Существуют самые различные виды металлорежущих станков, однако все они приведены в систему и классифицируются по различным признакам. В зависимости от вида обработки металлорежущие станки распределены в 9 групп:
1) токарные;
сверлильные и расточные;
шлифовальные, полировальные, заточные;
комбинированные;
зубо - и резьбообрабатывающие;
фрезерные;
строгальные, долбежные, протяжные;
разрезные;
разные.
Станки токарной группы наиболее распространены в машиностроении и металлообработке по сравнению с металлорежущими станками других групп.
Токарный станок позволяет выполнять следующие операции:
1. точение наружных поверхностей цилиндрических и конических;
2. растачивание внутренних цилиндрических и конических поверхностей;
3. подрезание торцов и уступов;
4. отрезание заготовки;
5. сверление отверстий;
6. нарезание внутренней и наружной резьбы.
В токарно-винторезном станке, как и в любой другой технологической машине (сверлильном станке, токарном станке по дереву и др.), есть электродвигатель, передаточный механизм, рабочий орган и система управления.
В передаточных механизмах применяются различные механические передачи.
ременная;
зубчатая;
реечная.
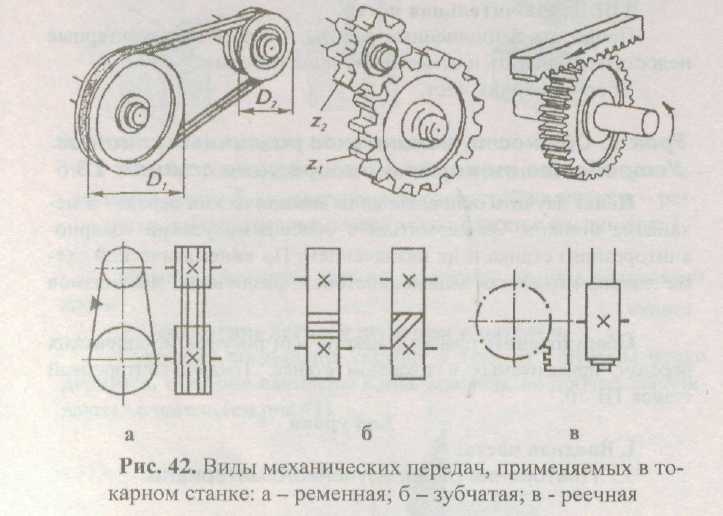
Деталь передачи, которая передает движение, называется ведущий шкив - Д, зубчатое колесо - Z (шестерня).
Деталь, которая воспринимает движение, называется ведомый шкив - Д2, шестерня -Z2.
Отношение частоты вращения ведущей детали к ведомой называется передаточное отношение. Оно составляет:
для ременной передачи U=Д1/Д2;
для зубчатой передачи U=Z1/Z2.
Принцип работы токарного станка заключается в том, что режущий инструмент снимает стружку с вращающейся заготовки. Для того, чтобы охватить резанием всю поверхность обрабатываемой детали, инструмент перемещают вдоль оси вращающейся заготовки.
УСТРОЙСТВО ТОКАРНО-ВИНТОРЕЗНОГО СТАНКА:
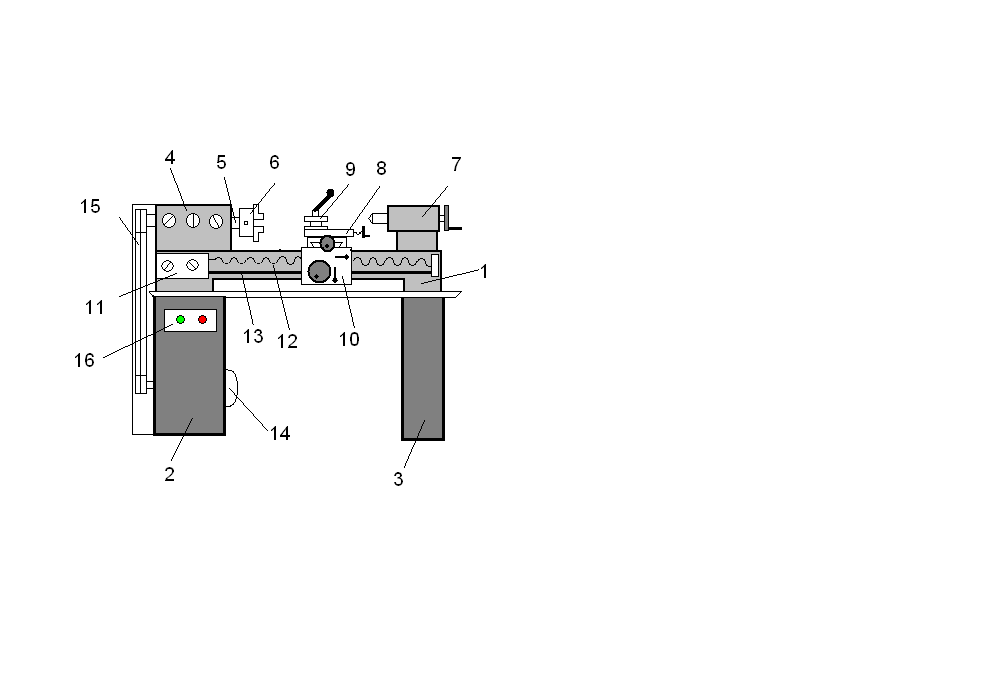
1. Станина
2. Передняя тумба
3. Задняя тумба
4. Передняя (шпиндельная) бабка
5. Шпиндель
6. Патрон
7. Задняя бабка
8. Суппорт
9. Резцедержатель
10. Фартук суппорта
11. Коробка подач
12. Ходовой винт
13. Ходовой вал
14. Электродвигатель
15. Ременная передача
16. Кнопочная станция Станина 1- основание станка, установленное на двух тумбах 2 и 3. Передняя (шпиндельная) бабка 4 установлена слева на станине. В ней размещен шпиндель 5, который передает вращение заготовке, закрепляемой в патроне 6. Также в передней бабке размещена коробка скоростей, предназначенная для изменения частоты вращения шпинделя. По направляющим станины передвигается и закрепляется в определенном положении задняя бабка 7. Задняя бабка служит для закрепления длинных заготовок, установки режущих инструментов. Она может перемещаться вдоль основания по направляющим станины и крепится к нему в необходимом положении. В верхней части корпуса бабки находится пиноль, которую можно передвигать вращением маховика и фиксировать в заданном положении соответствующей рукояткой. Суппорт 8 предназначен для закрепления и перемещения специальными рукоятками режущего инструмента. На верхних салазках суппорта установлен поворотный резцедержатель 9, предназначенный для закрепления режущего инструмента. Фартук суппорта 10, служит для перемещения резца вдоль оси вращения заготовки. Резец приводится в движение вручную, вращением соответствующей рукоятки, или механически, путем преобразования вращательного движения ходового вала 13 или ходового винта 12 в поступательное движение. Коробка подач 11 – это механизм, предназначенный для изменения скорости и направления подачи режущего инструмента. За счет переключения рукояток управления можно получать различные частоты вращения ходового винта или ходового вала и тем самым обеспечить различные скорости перемещения резца вдоль оси заготовки .При обработке заготовок на токарном станке различают два движения: 1. Главное движение – вращение заготовки – обеспечивается за счет передачи движения по цепи: двигатель – ременная передача – коробка скоростей – шпиндель с патроном и заготовкой. 2. Движение подачи (подача) – поступательное движение резца относительно заготовки. Подача бывает: 2.1. Продольная – перемещение резца вдоль оси заготовки. 2.2. Поперечная – перемещение резца перпендикулярно оси вращения заготовки. Движение подачи обеспечивается цепочкой: двигатель – ременная передача – коробка скоростей – коробка подач - фартук суппорта – суппорт с резцом. Или фартук – суппорт с резцом (при ручной подаче). Практическая работа: ознакомление учащихся с токарным станком, освоение различных приемов работы рукоятками и штурвалами управления станком.Тема: Технология токарных работ. Токарные резцы и их геометрия.Цель урока: ознакомить учащихся с видами токарных резцов, геометрии режущей части резцов, углах резания токарного резца и их влиянии на процесс резания.Оборудование: комплект токарных резцов, образцы работ, выполненные различными токарными резцами, плакаты.Содержание:При работе на токарном станке применяется различный режущий инструмент: резцы, сверла, метчики, плашки, развертки, накатки и пр. Резец – основной режущий инструмент для токарной обработки. Изготавливаются резцы из стали, по твердости превышающей обрабатываемый материал. Токарный резец представляет собой стержень прямоугольного сечения (тело резца), рабочая часть которого (головка) имеет режущие кромки в форме клина. Тело служит для закрепления в резцедержателе. Головка непосредственно участвует в процессе резания. В головке резца различают: 1. переднюю поверхность – по ней сходит стружка при резании; 2. главную заднюю поверхность; 3. вспомогательную заднюю поверхность; 4. главную режущую кромку – образуется пересечением передней и главной задней поверхностями; 5. вспомогательную режущую кромку – образуется пересечением передней и вспомогательной задней поверхностью. 6. вершину резца – образуется пересечением главной и вспомогательной режущих кромок. 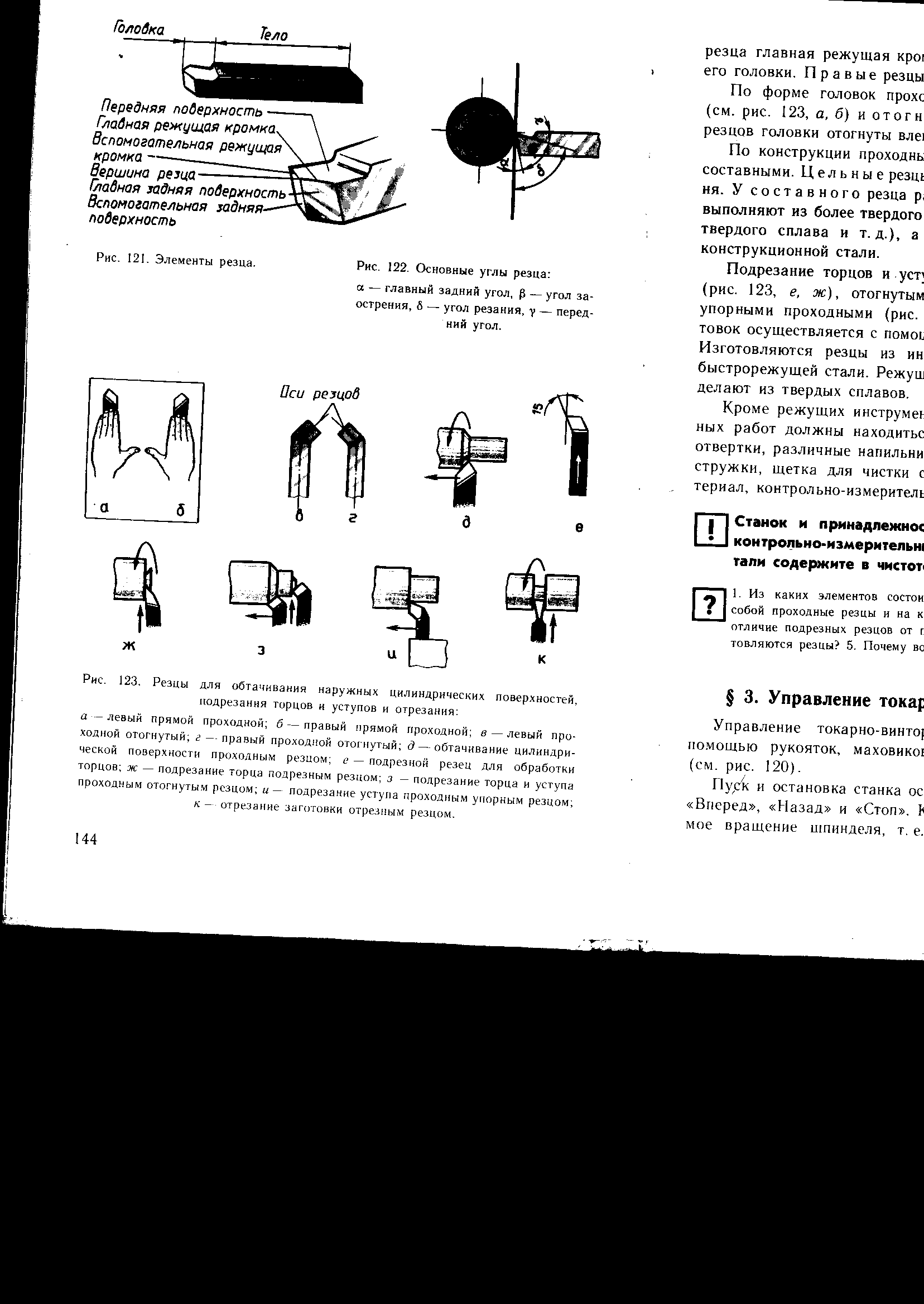 При резании металла токарным резцом различают три вида поверхностей: 1.обрабатываемую
2.поверхность резания
3. обработанную.
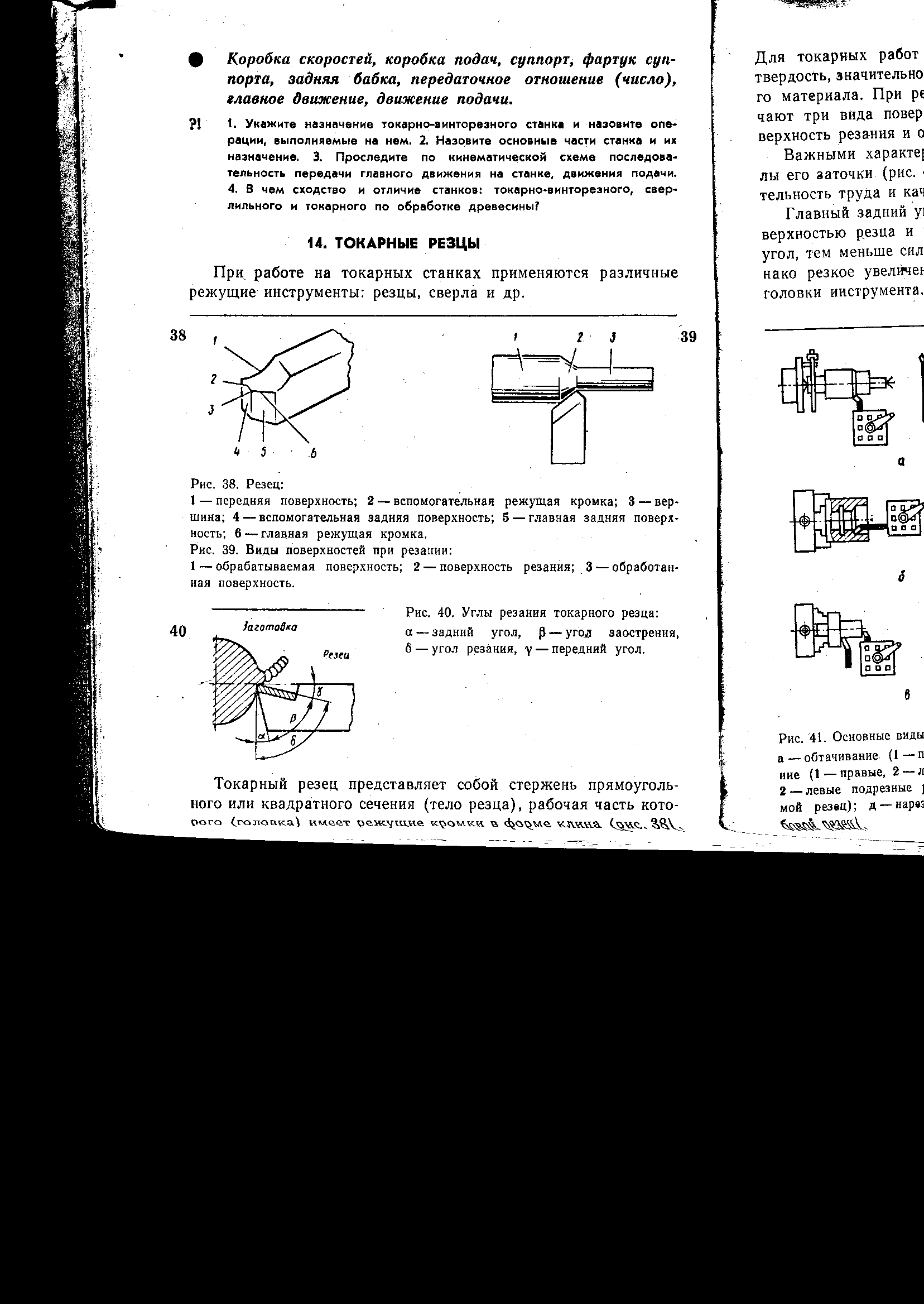 Важными характеристиками токарного резца являются углы его заточки, от них во многом зависит производительность труда и качество обработки. Главный задний угол - угол между главной задней поверхностью резца и плоскостью резания. Чем больше задний угол, тем меньше сила трения между резцом и заготовкой. Однако резкое увеличение заднего угла приводит к ослаблению головки инструмента. Передний угол - оказывает влияние на процесс резания, на легкость схода стружки, качество обработанной поверхности. Увеличение этого угла приводит к ослаблению головки инструмента. Угол заострения - угол между передней и главной задней поверхностями. Величина угла заострения определяет прочность и стойкость главной режущей кромки инструмента. При заточке резца этот угол обычно делают как можно больше. Угол резания - угол между передней поверхностью резца и плоскостью резания; он равен сумме углов заострения и главного заднего. Резцы классифицируют:1. по направлению подачи – правые и левые. 2. по конструкции головки – прямые, отогнутые, оттянутые. 3. по роду материала – из быстрорежущей стали, твердого сплава и тд. 4. по способу изготовления – цельные и составные. 5. по сечению стержня – прямоугольные, круглые, квадратные. 6. по виду обработки. По виду обработки резцы бывают: Практическая работа: изучение устройства токарных резцов. Определение назначения предложенных учащимся резцов. Определение с помощью угломера углы заточки резцов.Тема: Установка токарных резцов и заготовок.Цель урока: Научить учащихся правильно выбирать, устанавливать заготовки и токарные резцы для обработки на токарном станке.Оборудование: токарно-винторезный станок, комплект резцов, ключ для патрона станка, центр, заготовки, плакаты.Содержание:С действиями по управлению токарно-винторезным станком тесно связаны такие операции, как установка и закрепление на станке заготовок и режущих инструментов. С этих операций начинается любой вид токарной обработки. Приступая к работе, сначала проверяют качество заготовки (без раковин и прямые). Для выполнения основных токарных операций небольшие по размеру заготовки закрепляют в трехкулачковом самоцентрирующем патроне. Установка заготовок:1. сместить фартук вправо, все рукоятки и кнопки установить в нейтральное положение. 2. Ключом развести кулачки патрона. 3. Правой рукой установить заготовку в патрон на глубину не менее 20 – 25 мм и с вылетом не более 60 мм. 4. Вращением ключа зажать заготовку в патроне и вынуть ключ из патрона!5. Включить станок на прямое вращение. 6. Опираясь рукой с мелом на станину, подвести мел к заготовке до образования меловой риски. 7. Выключить станок и если риска не сплошная, то легкими ударами молотка сместить заготовку и окончательно закрепить. 8. Для снятия заготовки, вращением ключа развести кулачки патрона, поддерживая заготовку правой рукой. Установка резцов:При точении вершина резца должна находиться на оси центров. 1. Установить в пиноль задней бабки центр, выдвинуть пиноль задней бабки на 40-50 мм и зафиксировать ее. 2. Ослабить гайки крепления резца в резцедержателе. 3. Установить резец в резцедержателе перпендикулярно оси центров с вылетом от края поверхности резцедержателя на расстояние равное 1-1,5 высоты резца. 4. Предварительно закрепить резец в резцедержателе и подведите его вершину к центру пиноли. При необходимости отверните винты крепления резца и подложите под державку резца подкладки. 5. Окончательно закрепите резец и произведите пробную подрезку торца. Основные требования к безопасности работы на токарно-винторезном станке.1. Не включать станок без разрешения учителя. 2. Работать на станке только в специальной одежде. 3. Не оставлять ключ в патроне станка. 4. Не допускать «биения» заготовки в патроне станка. 5. Не хранить резцы «навалом». 6. Резцы использовать строго по назначению. 7. Подводить резец к заготовке только после включения станка. 8. Останавливать станок только после отвода резца от обрабатываемой заготовки. 9. Не передавать и не брать предметы через движущиеся части станка. 10. Во время работы не наклонять голову близко к вращающемуся патрону. 11. Не опираться на станок, не класть на него инструменты и заготовки. 12. Не отходить от включенного станка. 13. Не трогать руками или измерять заготовку, не выключив станка. 14. Нельзя брать стружку руками. Удалять стружку со станка щеткой-сметкой и металлическим крючком, только после остановки станка. 15. Переключать рукоятки изменения частоты вращения шпинделя, ходового винта и ходового вала производить только после выключения станка. Практическая работа: упражнения по установке токарных резцов и заготовок на станок.Тема: Режимы резания при точении.Цель урока: дать понятие о режимах резания, их влиянии на обработку заготовок и способах выбора правильных режимов резания.Оборудование: Токарно-винторезный станок, заготовки, плакаты.Содержание:Для выполнения операций по обработке металлов на токарном станке необходимо, чтобы заготовка совершала вращательное движение, а резец, касаясь заготовки режущей кромкой, перемещался вдоль заготовки и срезал слой металла. При обработке разных заготовок и различными инструментами скорости вращения заготовки и перемещение резца также будут различными. И 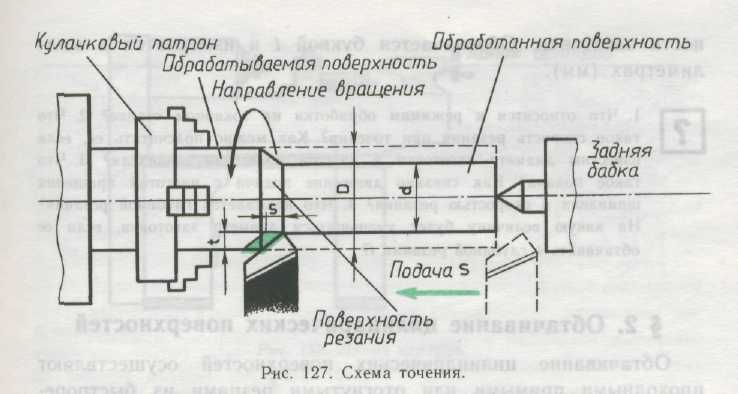 зменяется и толщина снимаемого с заготовки слоя металла. Все это отражается в режимах обработки. Режимы обработки на токарно-винторезном станке: 1. Скорость резания(V) – путь режущей кромки инструмента относительно обрабатываемой заготовки в направлении движения за единицу времени. Обозначается скорость резания буквой v и измеряется в метрах в минуту (м/мин). Скорость резания тесно связана с частотой вращения заготовки (п), которая измеряется в оборотах в минуту (мин -1). Зная частоту вращения и диаметр заготовки, можно подсчитать скорость резания. За один оборот заготовки точка обрабатываемой поверхности пройдет путь, равный длине окружности, диаметр которой равен диаметру заготовки. За несколько оборотов заготовки эта точка пройдет путь, равный нескольким длинам таких окружностей. V=D*n/1000, где D-диаметр заготовки, n-частота вращения шпинделя об/мин, 1000 – коэффициент перевода миллиметров в метры. Отсюда частота вращения шпинделя: n= * V/ D Подача — это величина перемещения резца за один оборот обрабатываемой заготовки. Она обозначается буквой s и измеряется в миллиметрах на один оборот заготовки (мм/об). Глубина резания - толщина снимаемого слоя металла, измеренная по перпендикуляру к обработанной поверхности заготовки. Обозначается буквой t и измеряется в мм. Чтобы во время работы не сломать резец, надо обеспечить плавную подачу резца и выбрать необходимую глубину резания. Установка глубины резания может производиться способом пробных стружек или с помощью лимба поперечной подачи. Способ пробных стружек заключается в следующем. Включается шпиндель станка. Вращением маховичка продольной подачи и рукоятки винта поперечной подачи вручную подводится резец к заготовке так, чтобы его вершина коснулась поверхности около самого торца. Установив момент касания, вращением маховичка продольной подачи резец отводят вправо от заготовки и с помощью рукоятки поперечной подачи устанавливают требуемую глубину резания. Затем ручной продольной подачей обтачивают заготовку на длине 3...5 мм (пробная стружка), возвращают резец вправо, останавливают станок и измеряют диаметр обработанной поверхности. Если диаметр больше требуемого, резец устанавливают на несколько большую глубину, снова снимают пробную стружку и повторяют измерение. Эти операции повторяют до тех пор, пока не получат заданный размер, после чего начинают обработку заготовки. По окончании обработки отводят резец назад и останавливают станок. В таком же порядке производится и чистовое точение. Для ускорения установки резца на требуемую глубину резания на современных токарных станках предусмотрено специальное приспособление— лимб поперечной подачи. Он представляет собой втулку или кольцо, по окружности которого нанесены деления, и располагается около рукоятки винта поперечной подачи. Деления отсчитываются по риске, находящейся на неподвижной втулке. В токарно-винторезном станке ТВ 6 цена деления лимба поперечной подачи равна 0,025 мм. Т.е. при перемещении лимба на одно деление резец будет подан на глубину резания, равную 0,025 мм, а диаметр наружной поверхности детали уменьшится не на 0,025, а на 0,025*2 мм, т.е. 0,05 мм. Общее число делений лимба Sп подачи резца определяется по формуле: Sп=D-d/2k, где D-диаметр заготовки, d-требуемый диаметр заготовки, k-цена деления лимба. Устанавливая резец на определенную глубину резания с помощью лимба поперечной подачи, нужно, однако, учитывать зазор между винтом и гайкой (люфт винта). Если данное обстоятельство упустить из виду, то величина перемещения резца может не соответствовать заданной по лимбу. Чтобы этого не произошло, необходимо всегда подводить требуемое деление лимба к риске правым вращением рукоятки винта. Практическая работа: упражнения по установке требуемой глубины резания при точении с помощью лимба поперечной подачи. Расчет требуемой глубины резания.Задачи: Вычислить общее число делений лимба поперечной подачи при точении заготовки диаметром 44,6; 28; 31,2; 8,3; 14,0; 100,6 мм для получения детали диаметром 40,2; 14,5; 22,8; 7,1; 12,1; 92,4 мм, если число делений лимба 0,025мм.Ответы: 88; 270; 168; 24; 38;164.Определить скорость резания заготовки диаметром 10, 18, 20,25,35, 50 мм при частоте вращения шпинделя 223, 177, 558, 382, 73, 318 об/ мин.Ответы:7, 10, 35, 30, 8, 50.Определить частоту вращения шпинделя для точения заготовки диаметром 15, 18, 22, 28, 30, 80 мм при скорости резания 3, 6, 10, 18, 20, 65 м/ мин.Ответы: 64, 106, 145, 170, 212, 259 об/мин.Тема: Обтачивание наружных цилиндрических поверхностей.Цель урока: ознакомить учащихся с приемами точения цилиндрических поверхностей на токарно-винторезном станке, возможном браке и способах его предупреждения.Оборудование: ТВ станок, комплект токарных резцов, инструкционные карты, чертежи, плакаты.Содержание:Для наружного продольного точения применяют проходные резцы. Проходные резцы бывают прямые, отогнутые и упорные. По направлению подачи – левые и правые. Глубину резания определяют в основном припуском на обработку, который выгодно удалять за один рабочий ход. Для уменьшения влияния сил резания иногда разделяют припуск на несколько рабочих ходов: 60% - при черновой обработке (10 делений лимба) 20 – 30 % - при получистовой обработке 10 – 20 – при чистовой обработке; При чистовом точении получают поверхности с малой шероховатостью, точные по форме и размерам. Подачу выбирают из справочников и корректируют по кинематическим данным станка. Скорость резания зависит от конкретных условий обработки. При точении длинных заготовок, один конец заготовки поддерживается центром задней бабки станка. Во время работы необходимо выключать станок и измерять диаметр заготовки штангенциркулем в нескольких местах. При обтачивании цилиндрических поверхностей возможны следующие виды брака:
|
|
|