|
Часть поверхности детали осталась необработанной. Здесь возможен ряд причин: из-за недостаточных размеров заготовки (малого припуска на обработку), кривизны заготовки, неправильной ее установки и неточной выверки.
Неправильные размеры обточенной поверхности. Причины: неточная установка резца на глубину резания или неправильное измерение детали при снятии пробной стружки.
Неровность обработанной поверхности. Причин этого может быть несколько: большая подача резца, дрожание резца из-за большого вылета или недостаточно прочного закрепления его в резцедержателе, дрожание детали вследствие непрочного закрепления ее или биения шпинделя.
Практическая работа: подготовка рабочего места токаря, изучение чертежей и технологической карты, точение цилиндрических поверхностей.
Тема: Подрезка торцов, уступов и отрезка заготовок на токарно-винторезном станке.
Цель урока: дать понятие об уступе, обучить приемам подрезки торцов заготовок, вытачивании уступов и выступов, а также отрезании заготовки.
Оборудование: ТВ станок, комплект токарных резцов, инструкционные карты, чертежи, плакаты.
Содержание:
Уступ – поверхность заготовки, образованная достаточно быстрым переходом от одного размера диаметра к другому (от меньшего к большему и наоборот).
Во многих случаях уступы специально не точат, они получаются во время обтачивания цилиндрических поверхностей, и его наклон соответствует наклону главной режущей кромки резца.
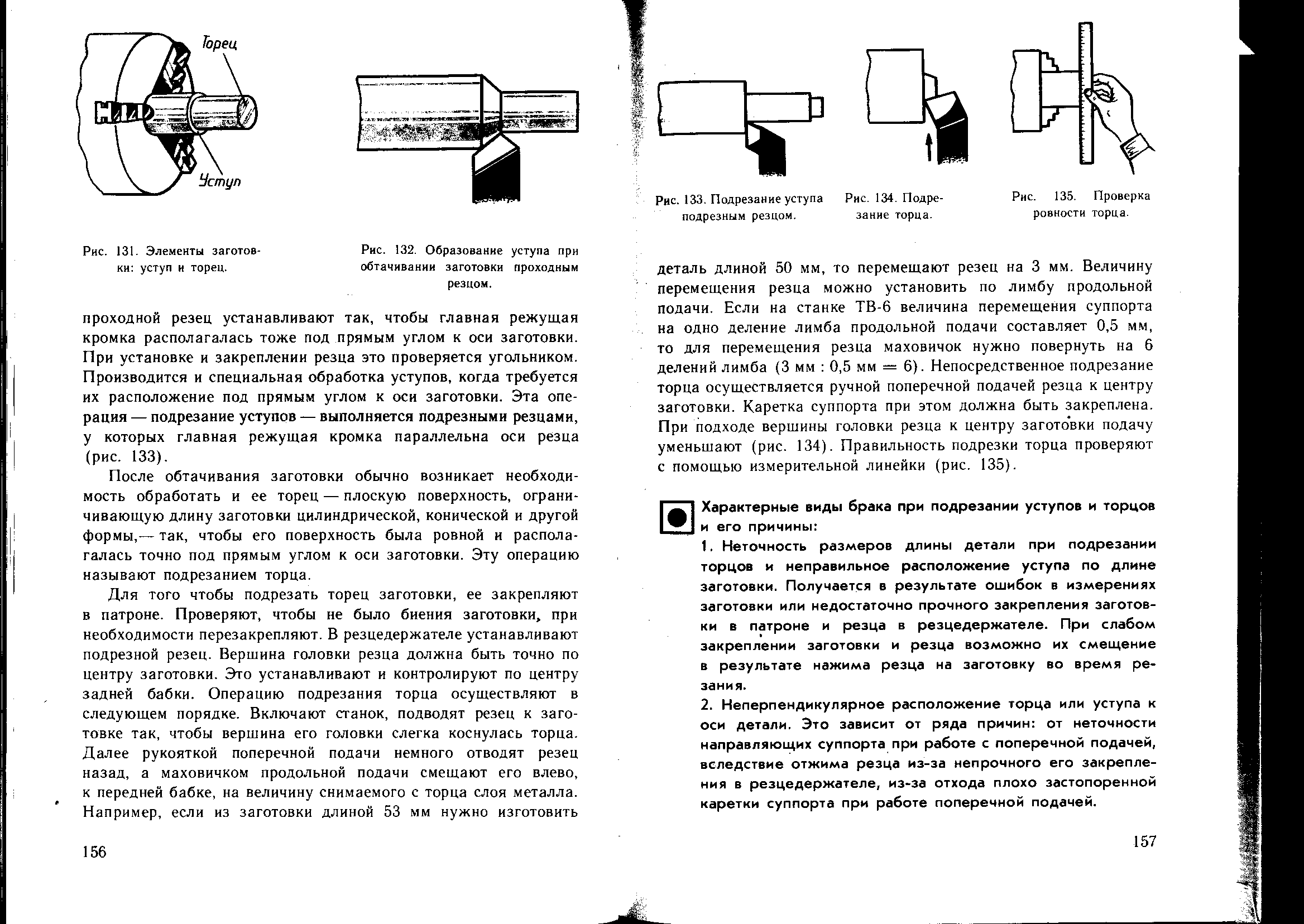
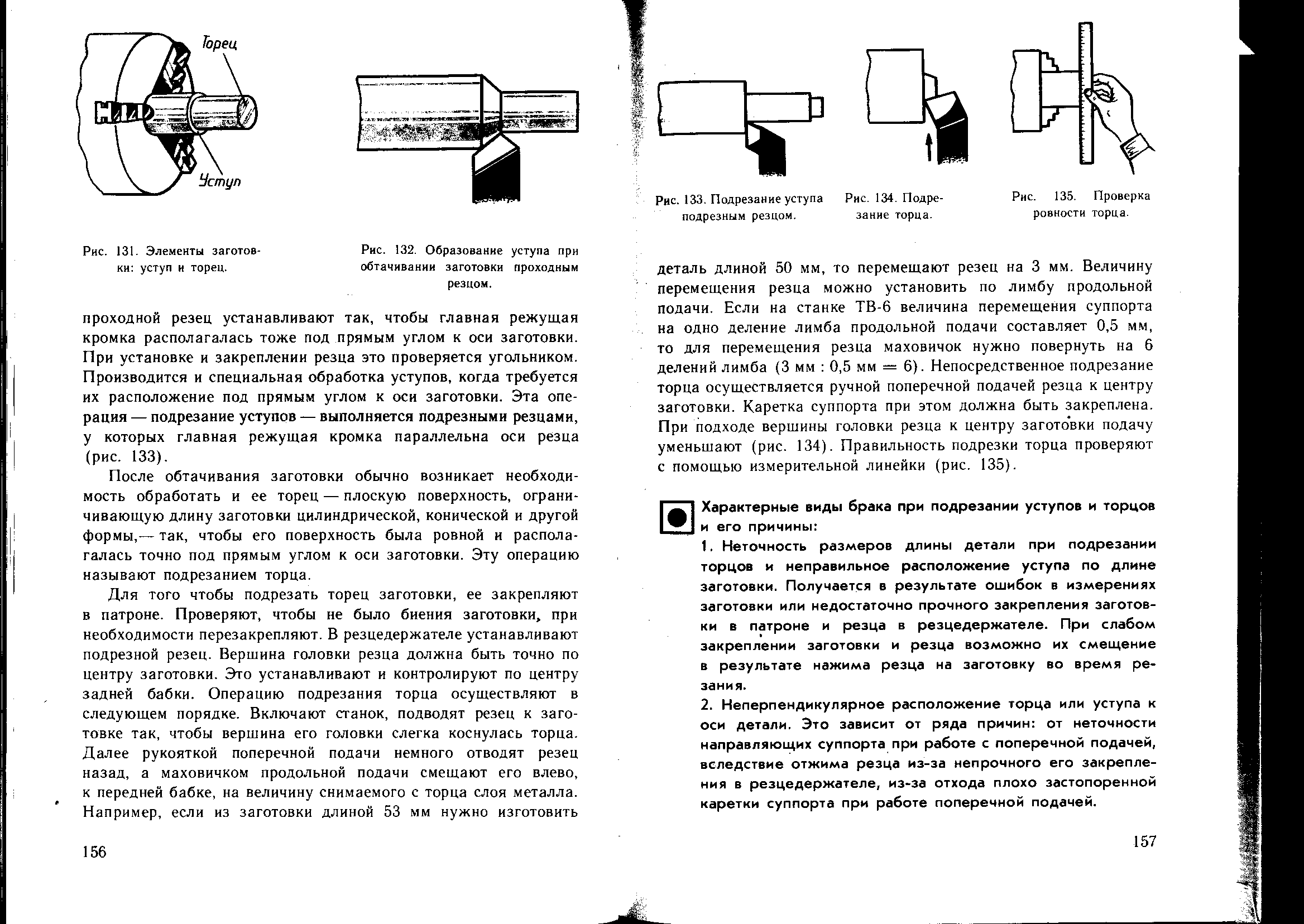
После обтачивания заготовки обычно возникает необходимость обработать ее торец – плоскую поверхность, ограничивающую длину заготовки цилиндрической, конической и другой формы, - так чтобы его поверхность была ровной и располагалась точно под прямым углом к оси заготовки.
Резцы для подрезания торцов устанавливают точно на оси центров, иначе на детали останется выступ.
Операцию подрезания торца осуществляют в следующем порядке:
1. Включают станок, подводят резец к заготовке так, чтобы вершина его головки слегка коснулась торца.
2. Рукояткой поперечной подачи немного отводят резец назад, а маховичком продольной подачи смещают его влево, к передней бабке, на величину снимаемого с торца слоя металла. Например, если из заготовки длиной 53 мм нужно изготовить деталь длиной 50 мм, то перемещают резец на 3 мм. Величину перемещения резца можно установить по лимбу продольной подачи. Если на станке ТВ-6 величина перемещения суппорта на одно деление лимба продольной подачи составляет 0,5 мм, то для перемещения резца маховичок нужно повернуть на 6 делений лимба (3 мм: 0,5 мм =6).
3. Подрезать торец ручной поперечной подачей резца к центру заготовки. Каретка суппорта при этом должна быть закреплена. При подходе вершины головки резца к центру заготовки подачу уменьшают. Правильность подрезки торца проверяют с помощью измерительной линейки.
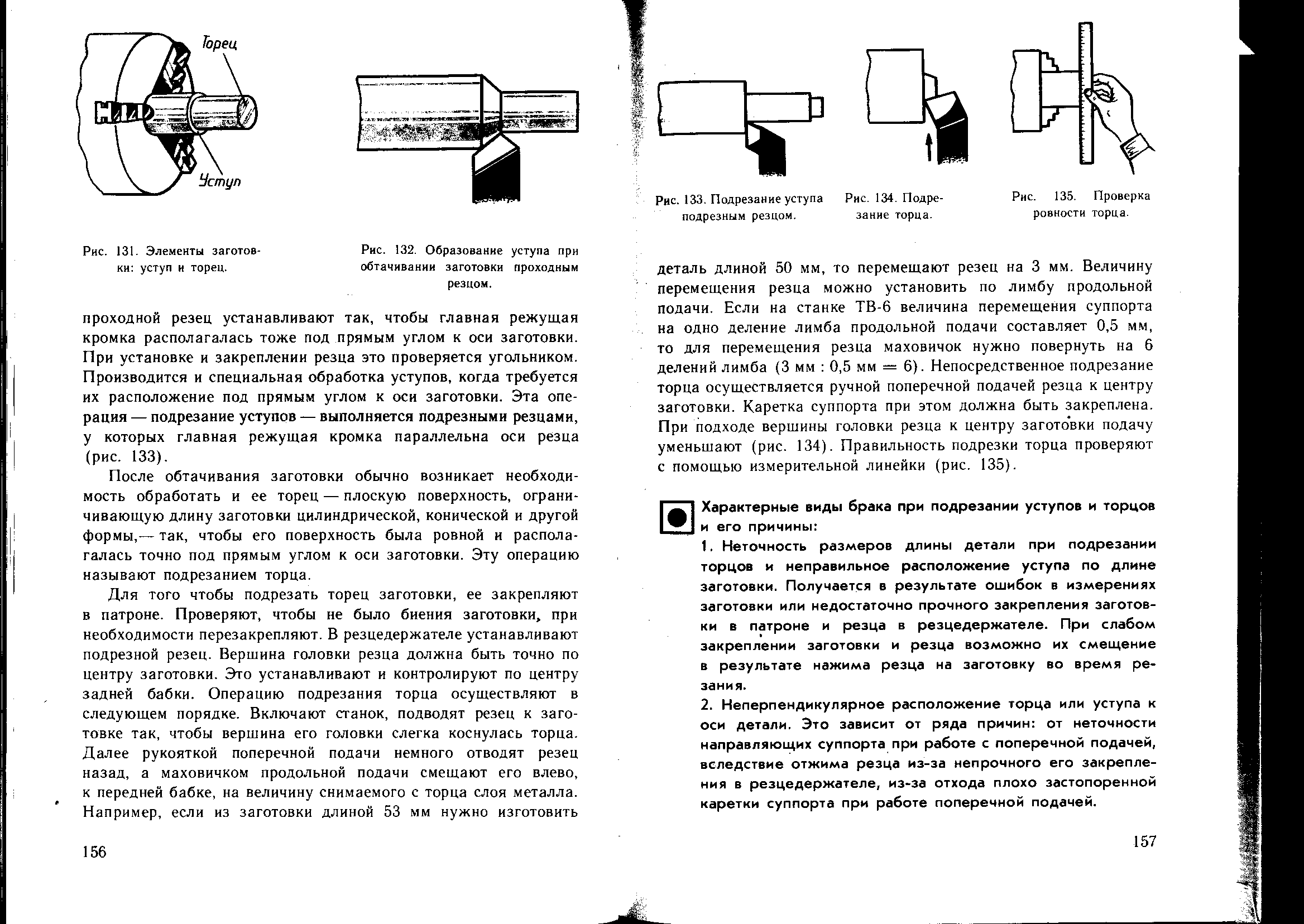
Характерные виды брака при подрезании уступов и торцов и его причины:
Неточность размеров длины детали при подрезании торцов и неправильное расположение уступа по длине заготовки. Получается в результате ошибок в измерениях заготовки или недостаточно прочного закрепления заготовки в патроне и резца в резцедержателе. При слабом закреплении заготовки и резца, возможно, их смещение в результате нажима резца на заготовку во время резания.
Неперпендикулярное расположение торца или уступа к оси детали. Это зависит от ряда причин: от неточности направляющих суппорта при работе с поперечной подачей, вследствие отжима резца из-за непрочного его закрепления в резцедержателе, из-за отхода плохо застопоренной каретки суппорта при работе поперечной подачей.
При изготовлении многих деталей на токарных станках применяется отрезание заготовок.
Эта операция производится отрезными резцами.
Отрезной резец имеет две вершины. Для уменьшения трения между резцом и разрезаемым материалом головка резца сужается к стержню под углом 1-20.
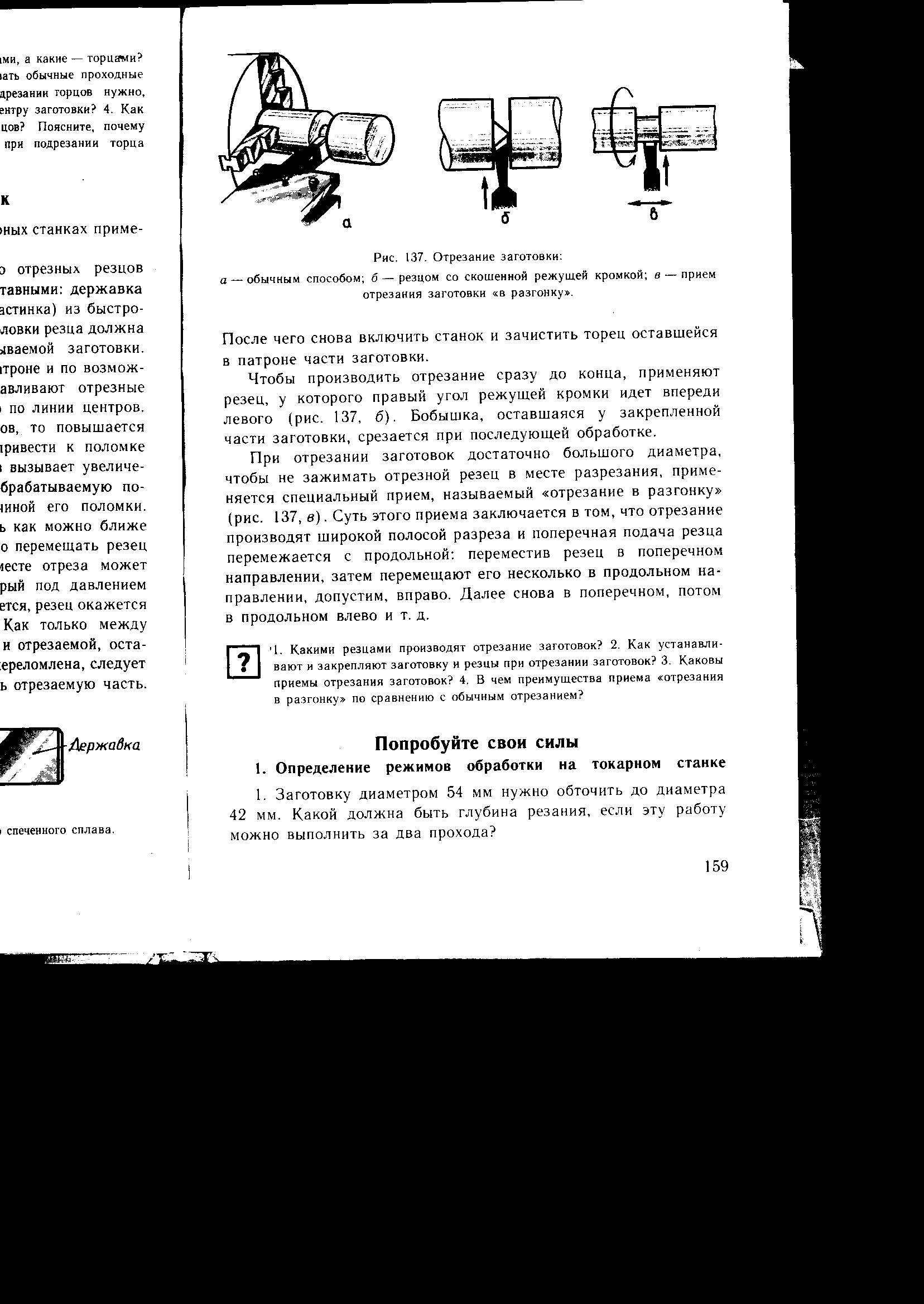
Порядок отрезания заготовок:
1. Отрезание заготовки следует производить как можно ближе к кулачкам патрона.
2. Не следует перемещать резец до самого центра заготовки, т.к. это может привести к его защемлению и поломке. Как только между разрезаемыми частями заготовки образуется тонкая перемычка, следует вывести резец, остановить станок и отломить заготовку.
3. Для полного отрезания заготовки, применяют резец, у которого правый угол режущей кромки идет впереди левого.
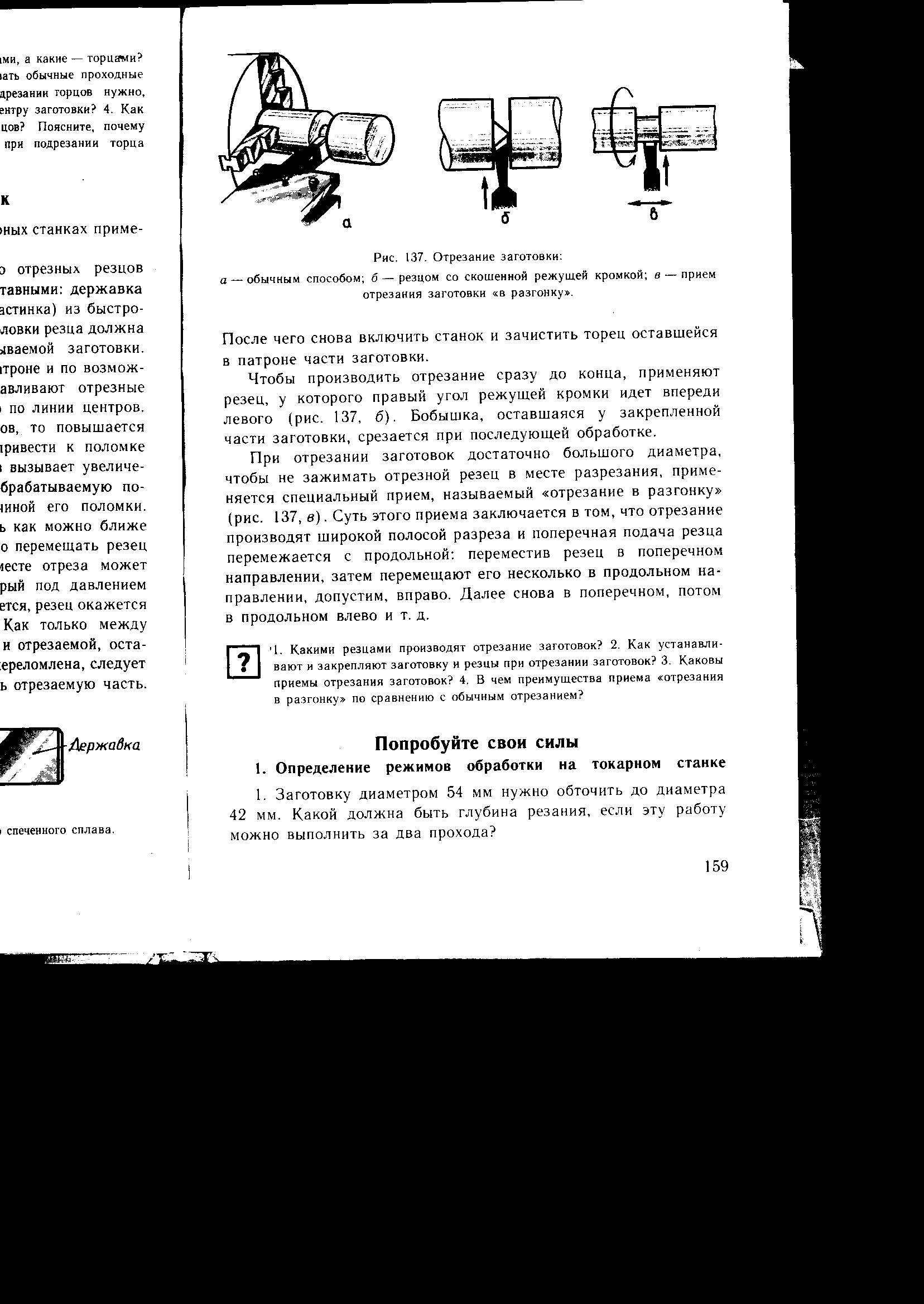
4. Для отрезания заготовки достаточно большого диаметра, чтобы не зажимать резец в месте резания, применяется специальный прием, называемый «отрезание в разгонку». Отрезание производится широкой полосой разреза, и поперечная подача резца совмещается с продольной.
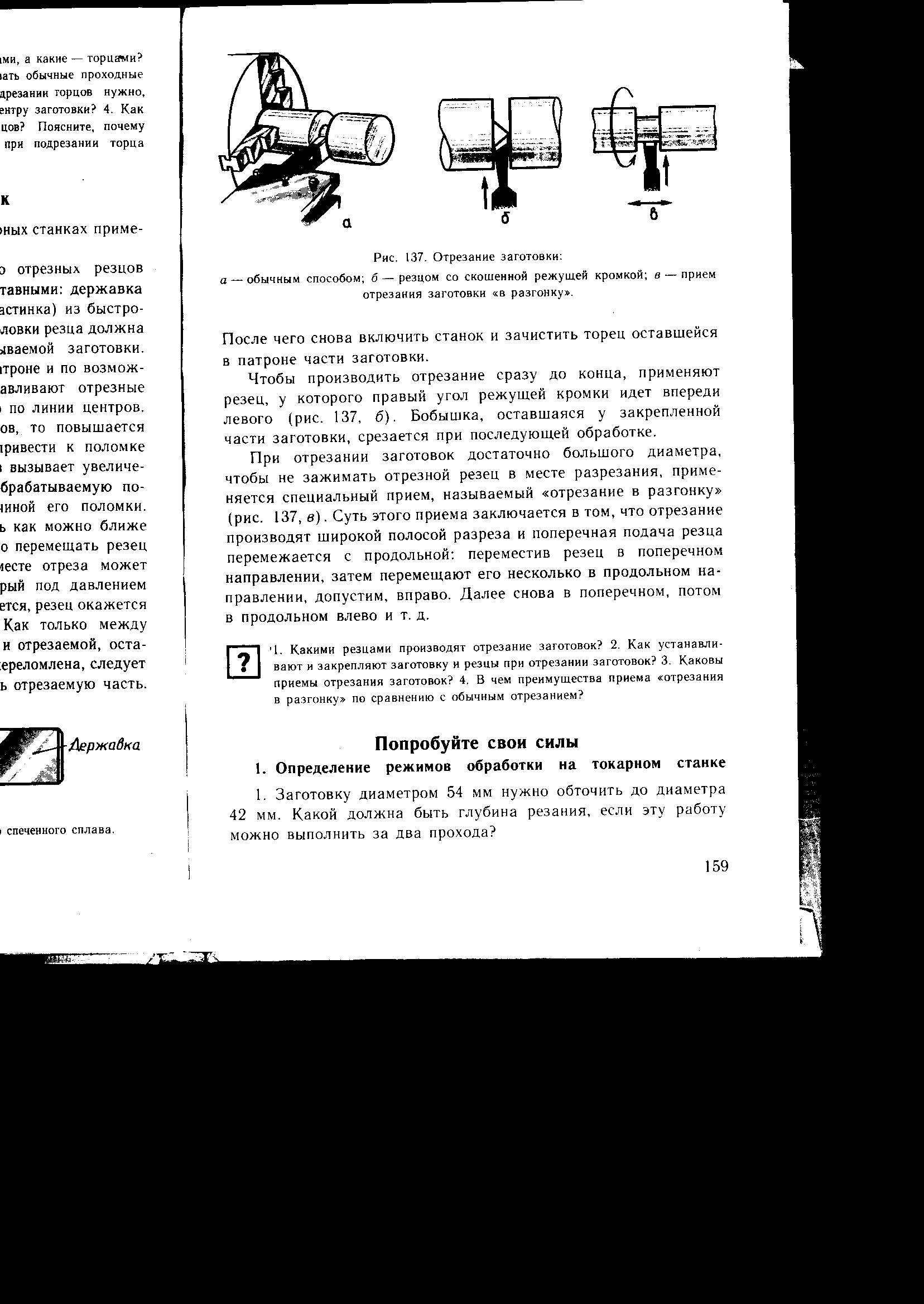
Практическая работа: организация рабочего места, изучение технологической карты, расчет припуска на обработку, точение детали.
Тема: Понятие о резьбе и ее элементах.
Цель урока: дать понятие о резьбе, ее элементах, классификации резьб.
Оборудование: модель образования винтовой линии, образцы с различными видами резьб, плакаты.
Содержание:
Наиболее распространенными соединениями деталей машин являются резьбовые. Широкое применение резьбовых соединений в машинах и механизмах объясняется их простотой и надежностью» удобством регулирования затяжки, а также возможностью их разборки и повторной сборки без замены детали.
Резьба бывает наружной и внутренней. Деталь (стержень) с наружной резьбой называется винтом, а с внутренней — гайкой.
Эти резьбы изготовляют на станках и вручную с помощью метчиков и плашек.
Основная задача при изготовлении болтов и гаек состоит в получении правильной винтовой линии.
Винтовая линия образуется следующим образом. Возьмем цилиндр и будем его равномерно вращать, приставив к его концу карандаш. Медленно передвигая карандаш от одного конца цилиндра к другому, мы получим на поверхности цилиндра линию, идущую по спирали, которая называется винтовой линией.
Если по направлению винтовой линии нарезать канавку, то получится резьба.
В зависимости от направления подъема витков на цилиндрической поверхности резьба может быть правой и левой.
Основные элементы резьбы:
1. Профиль резьбы – можно увидеть, если смотреть на винт сбоку, либо мысленно разрезать болт или гайку по их оси.
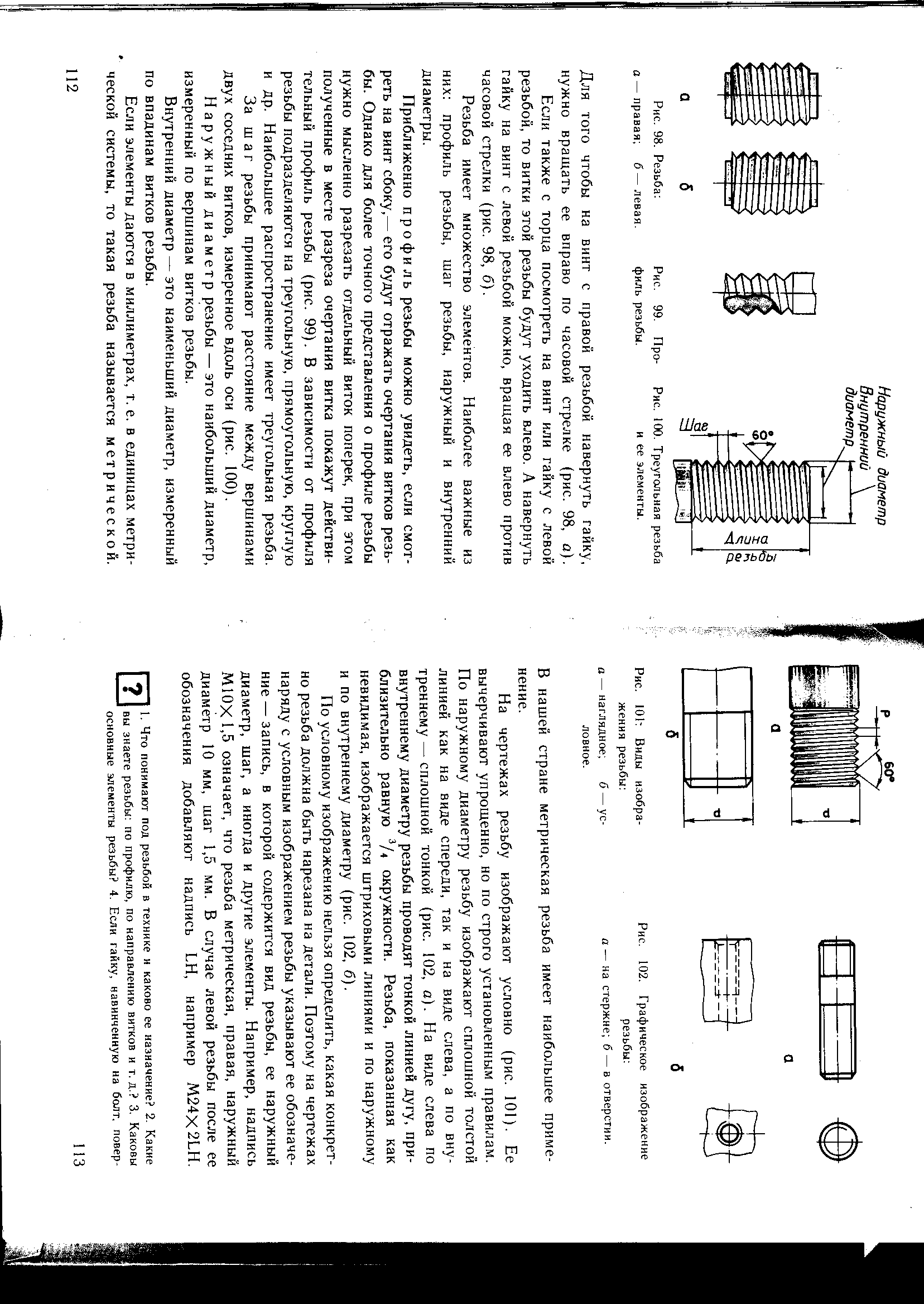
2. Виток (нитка) резьбы – часть резьбы, образуемая при одном полном обороте профиля.
3. Угол профиля – угол между боковыми сторонами профиля резьбы (у метрической 600, у дюймовой 550)
4. Высота (глубина резьбы) и профиля – расстояние от вершины резьбы до основания профиля, измеренное перпендикулярно оси болта.
5. Шаг резьбы – расстояние между параллельными сторонами или вершинами двух рядом лежащих витков, измеренное вдоль оси резьбы.
( Метрическая – измеряется в мм, дюймовая – количество витков в одном дюйме).
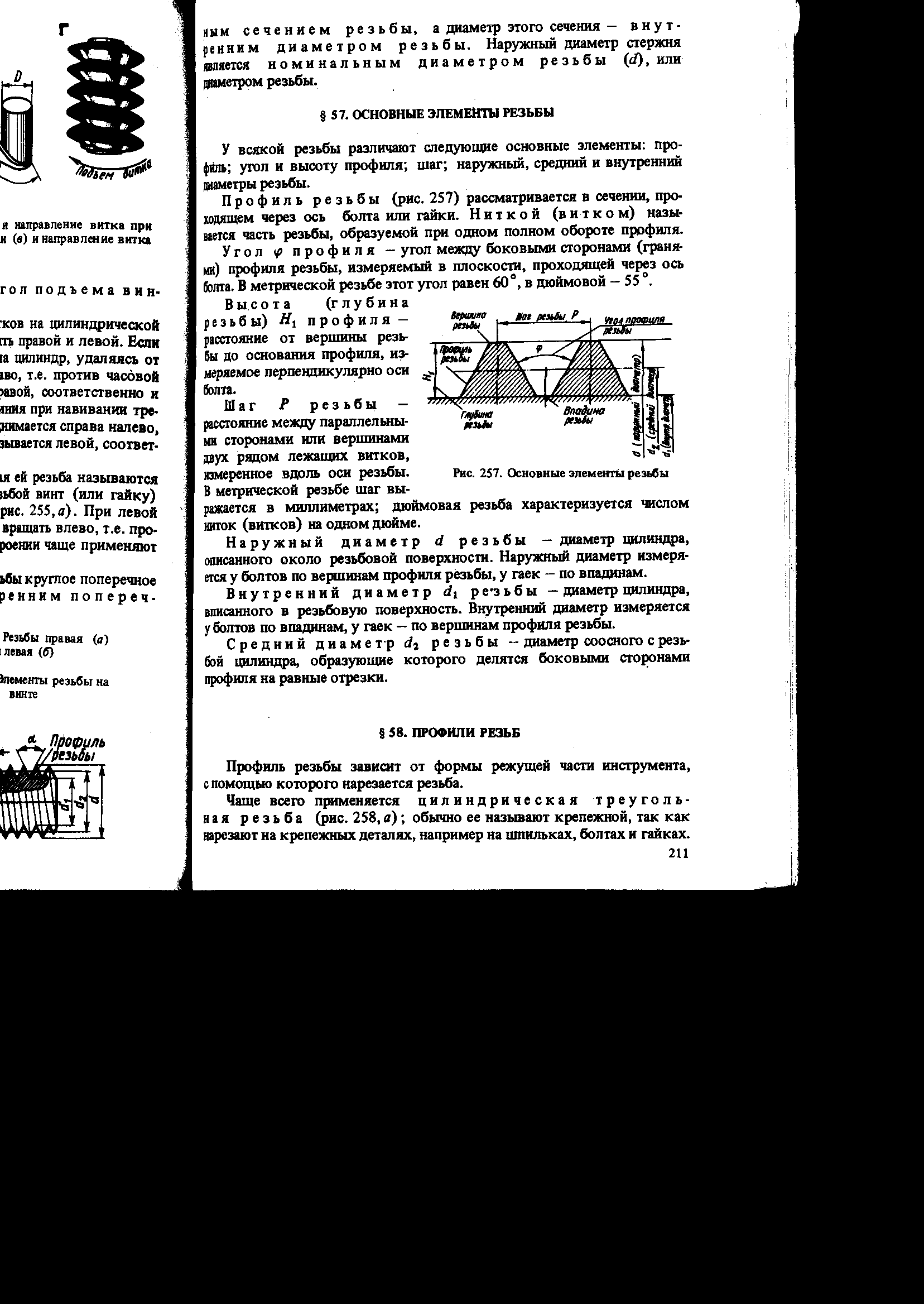
6. Наружный диаметр резьбы – у гаек измеряется по впадинам профиля, у болтов по вершинам.
7. Внутренний диаметр резьбы – измеряется у болтов по впадинам профиля, у гаек по вершинам профиля резьбы.
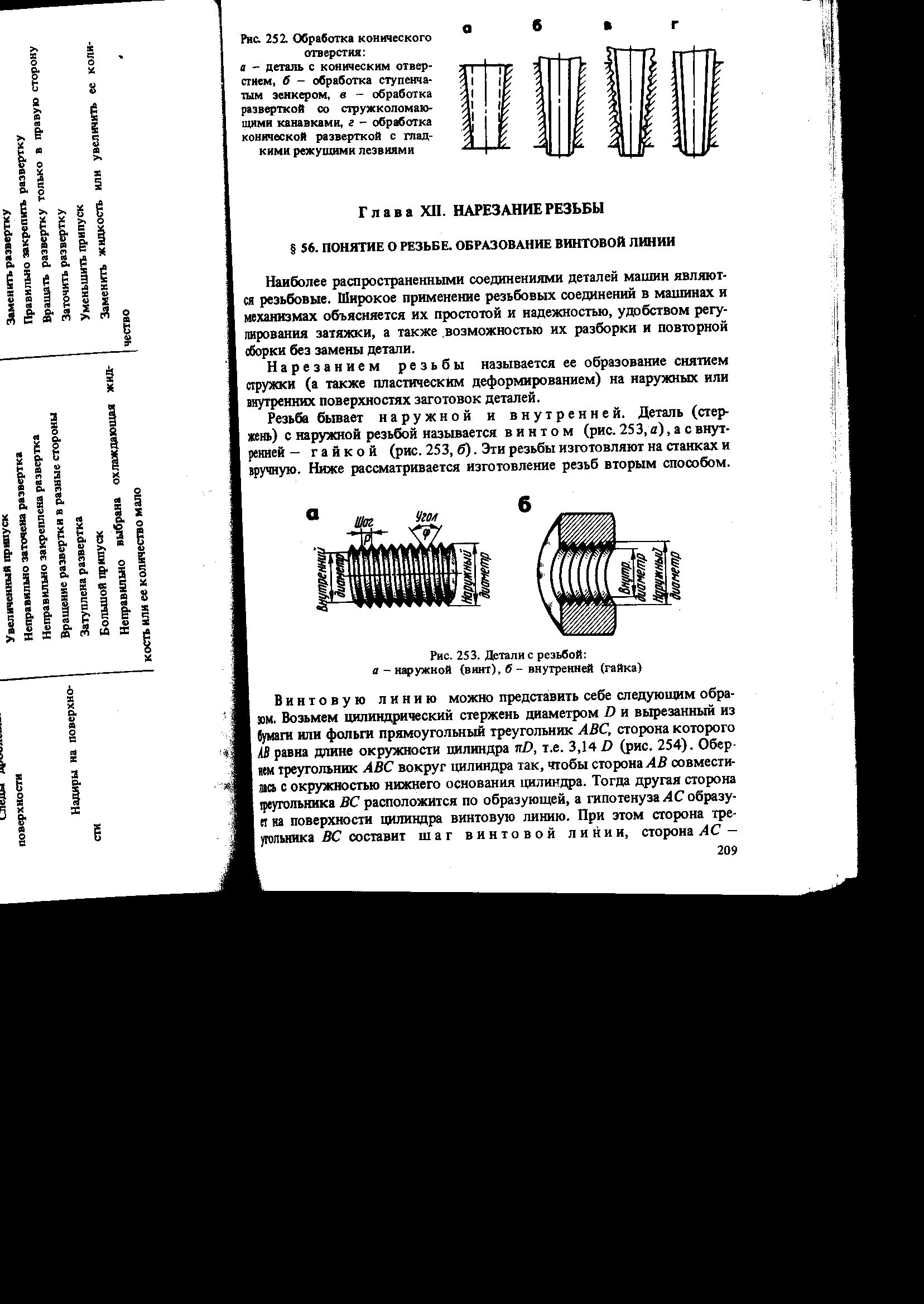
Основные профили резьб:
Профиль резьбы зависит от формы режущей части инструмента, с помощью которого нарезается резьба.
1. Цилиндрическая треугольная резьба – самая распространенная резьба, обычно ее называют крепежной, т.к. нарезают на крепежных деталях, болтах, гайках, шпильках.
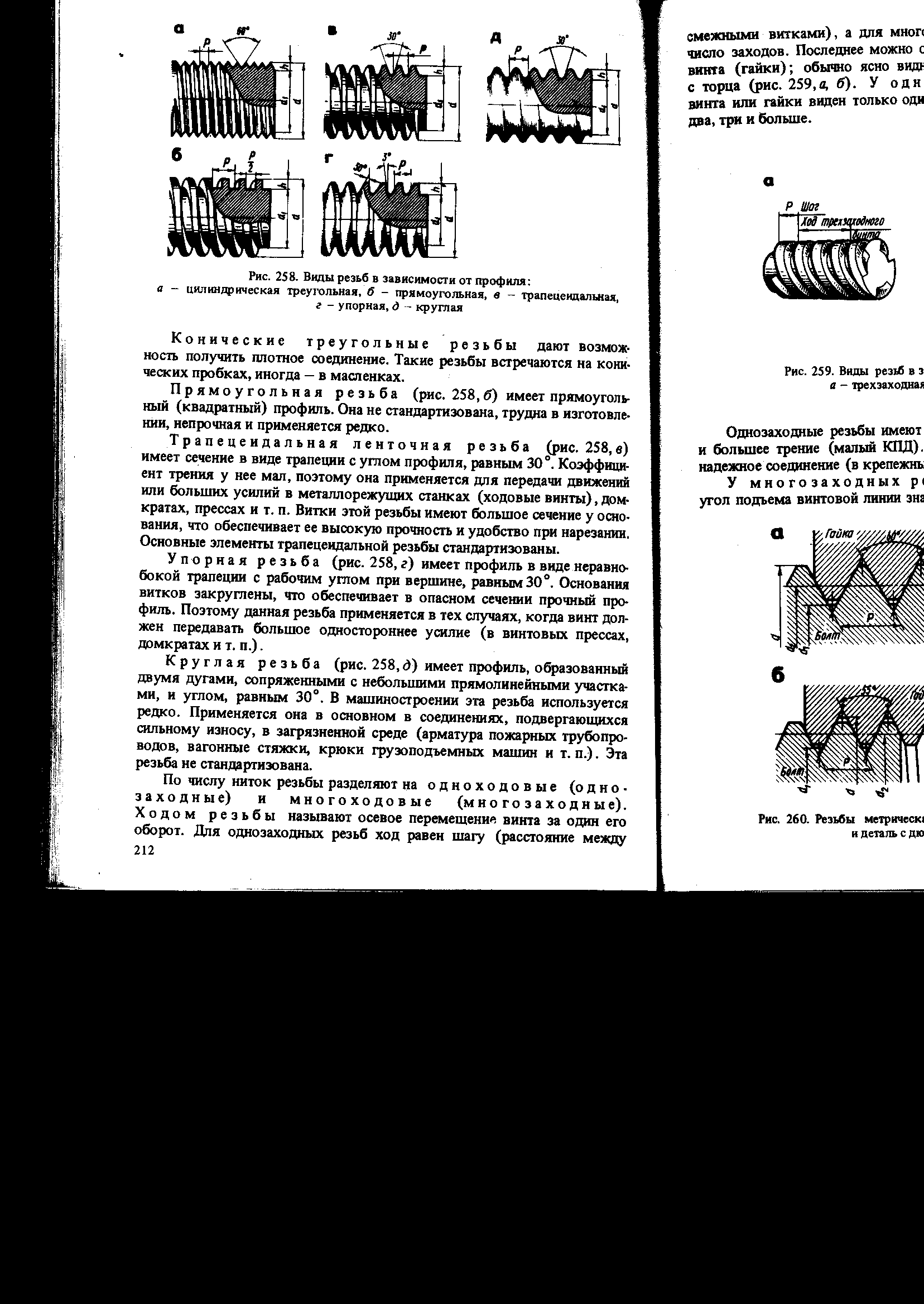
2. Трапецеидальная резьба – имеет сечение в виде трапеции с углом профиля 300. Коэффициент трения ее мал, поэтому она применяется для передачи движений или больших усилий в металлорежущих станках (ходовые винты), домкратах, прессах.
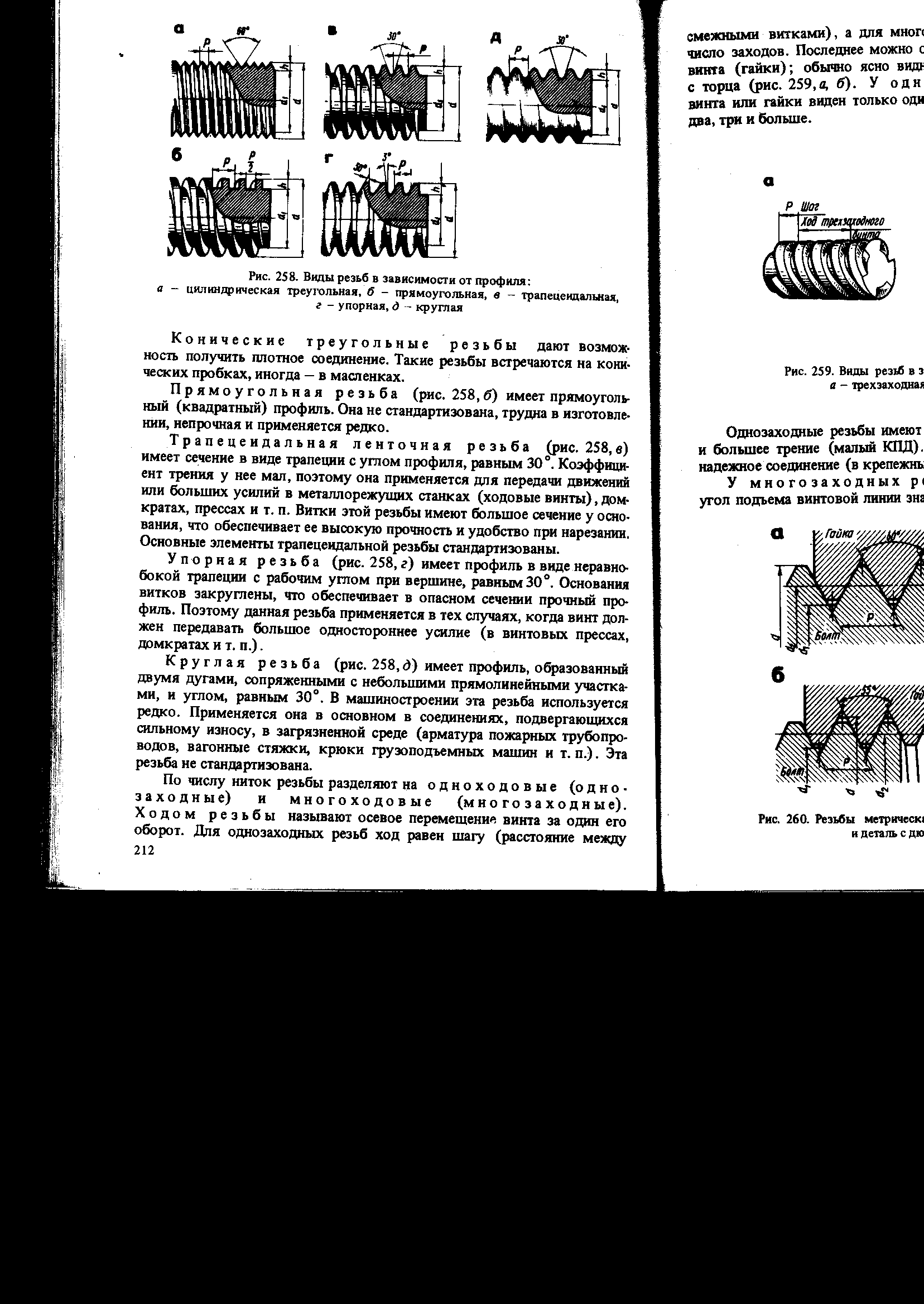 3. Упорная резьба – имеет профиль в виде неравнобокой трапеции с рабочим углом при вершине, равным 300. Эта резьба применяется в тех случаях, когда винт должен передавать большое одностороннее движение (в винтовых прессах, домкратах, и пр.).
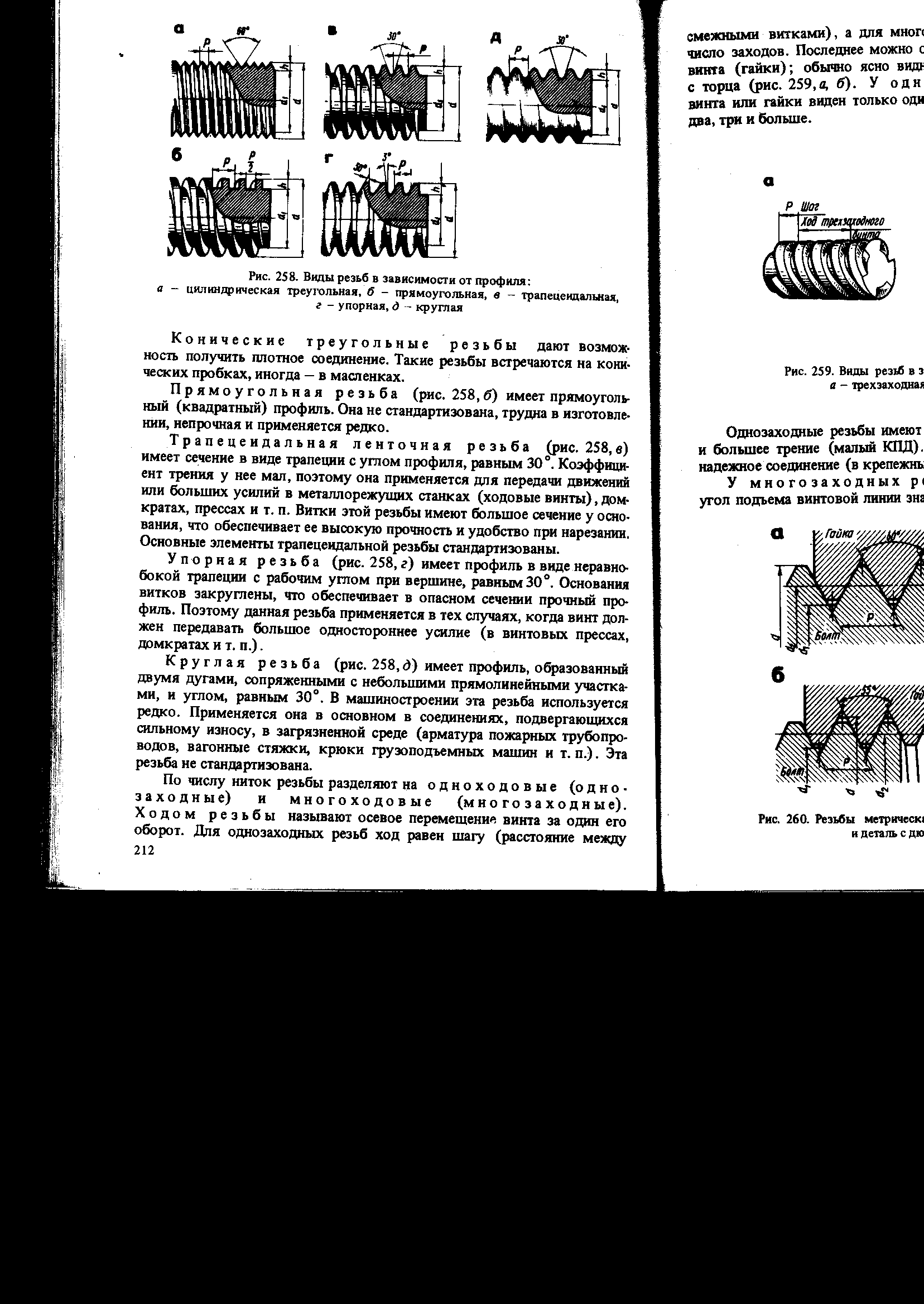
4. Круглая резьба – имеет профиль, образованный двумя дугами, сопряженными с небольшими прямолинейными участками, и, углом, равным 300. В машиностроении используется редко. Применяется в соединениях, подвергающихся сильному износу, в загрязненной среде.
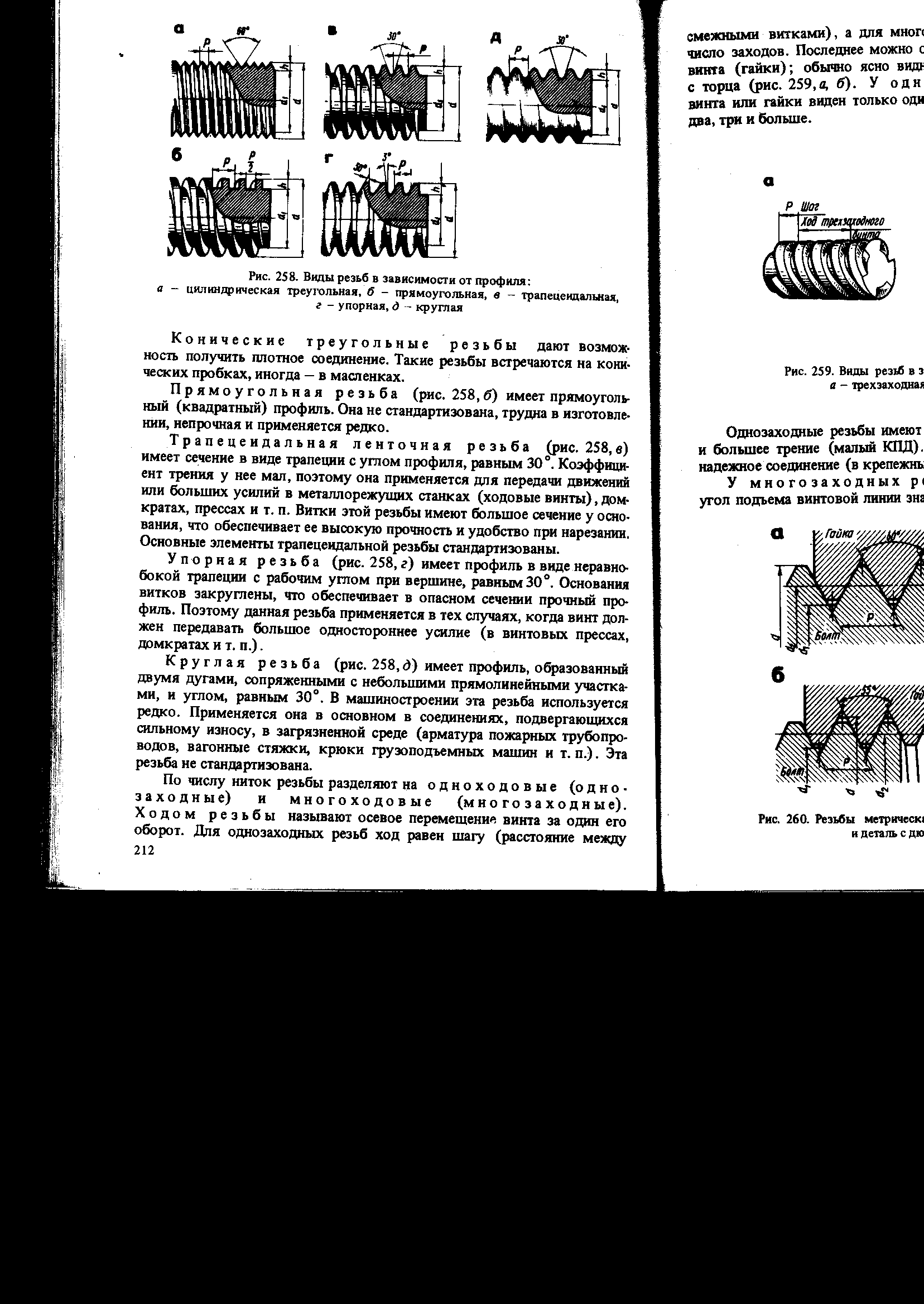
5. Прямоугольная резьба – имеет прямоугольный (квадратный профиль). Она трудна в изготовлении, непрочная и применяется редко.
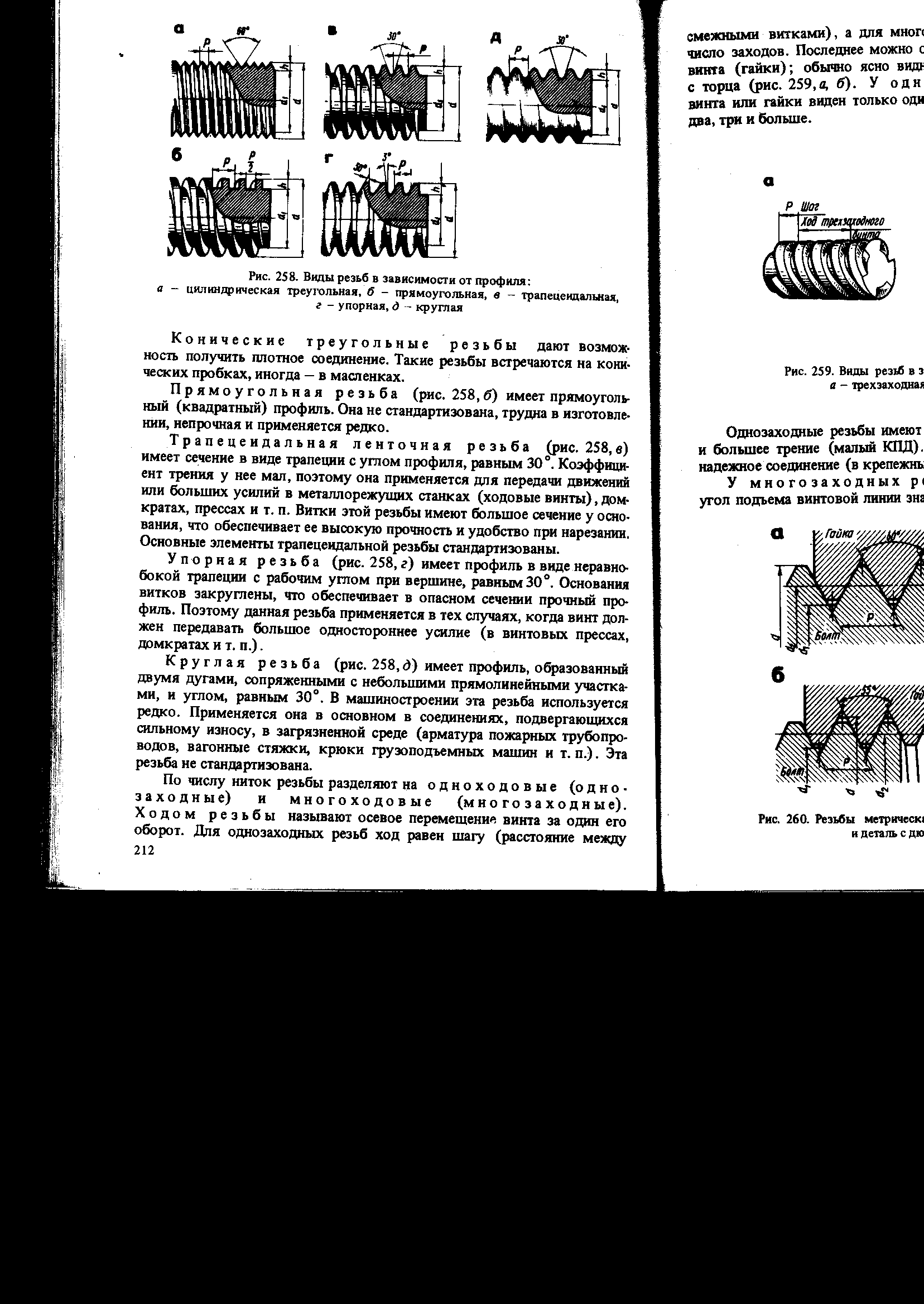 На чертежах резьбу изображают условно. Ее вычерчивают упрощенно, но по строго установленным правилам.
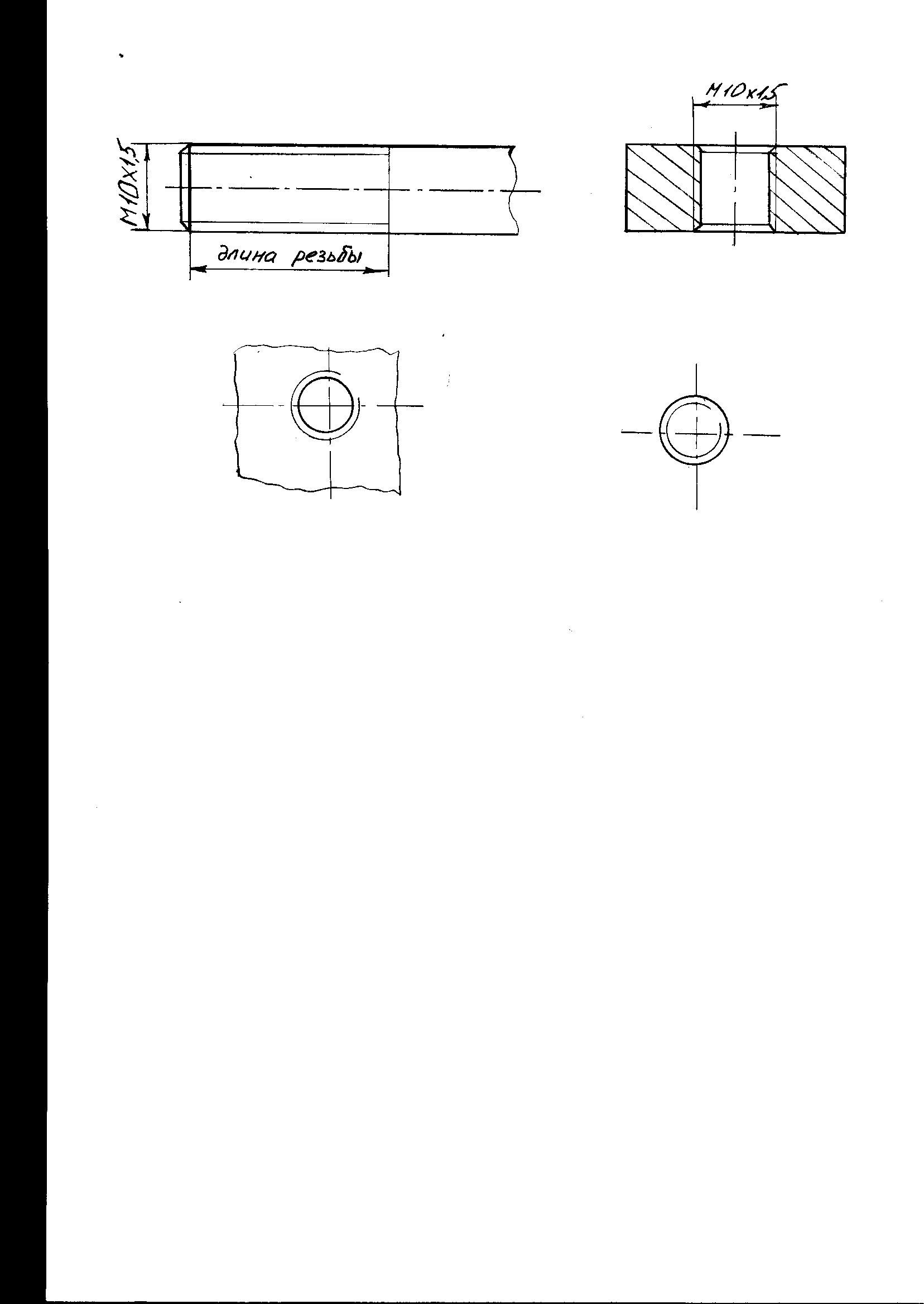
Практическая работа: изучение типов резьб по образцам, составление чертежей с деталей, содержащих ту или иную резьбу. Тема: Нарезание наружной резьбы.
Цель работы: дать понятие о процессе нарезания наружной резьбы, об инструментах, используемых для этого и приемах работы, а также о возможном браки и мерах его предупреждения.
Оборудование: заготовки, круглые, разрезные, раздвижные, плашки, клупп, таблицы
Содержание:
Нарезанием резьбы называется её образование снятием стружки (а также пластическим деформированием) на наружных или внутренних поверхностях заготовок деталей. Для нарезания наружной резьбы используют специальный резьбонарезной инструмент – плашки. Их изготавливают из твердой инструментальной стали.
В зависимости от конструкции плашки делят:
1. Круглые плашки (лерки) изготавливают двух видов:
1.1 Цельная плашка – стальная закаленная гайка, в которой через резьбу прорезаны сквозные продольные отверстия, образующие кромки и служащие для выхода стружки.
С обеих сторон плашки имеются заборные части.
Их применяют при нарезании резьб до диаметра 52 мм.
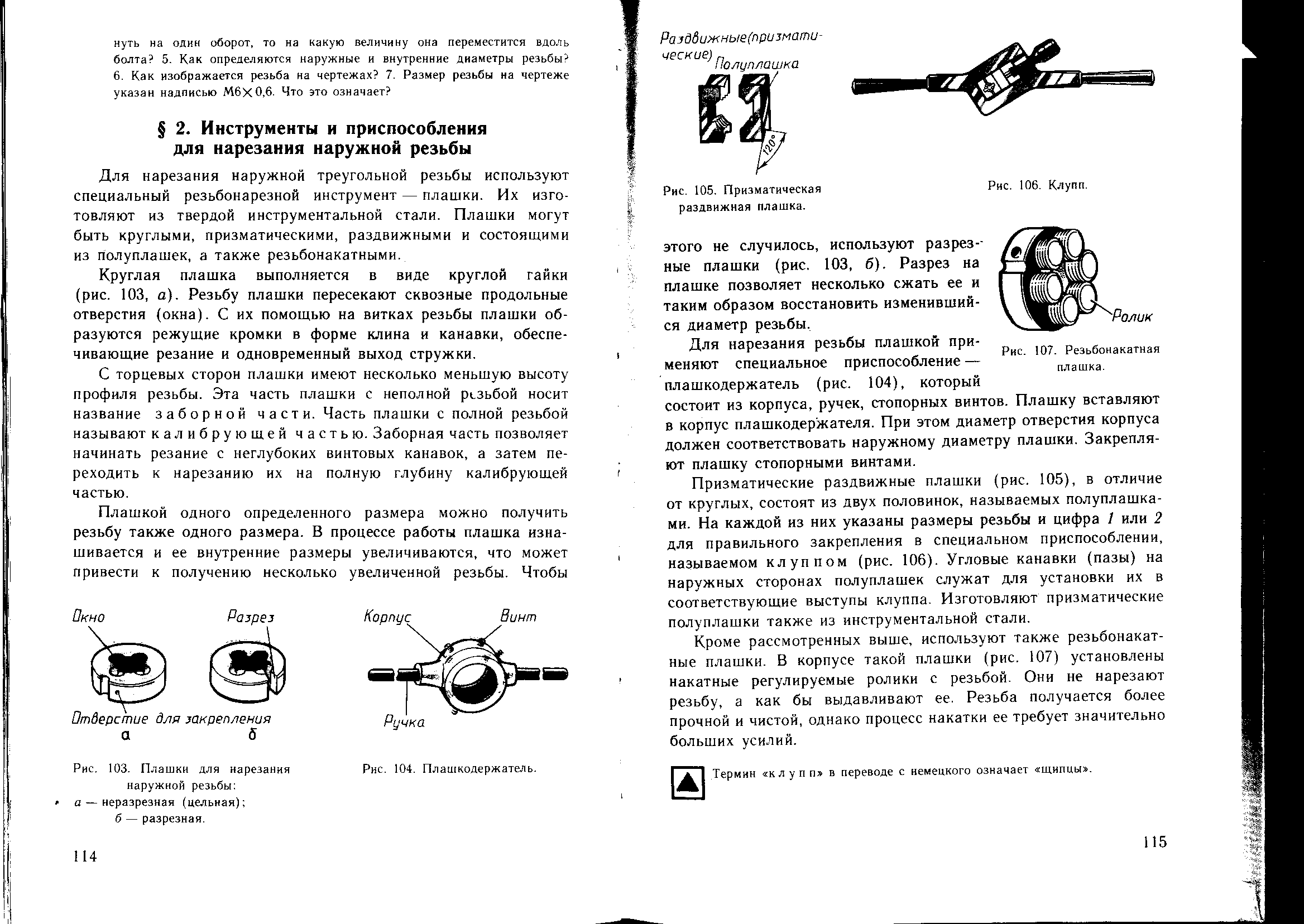
При нарезании резьбы их закрепляют в специальных воротках – плашкодержателях.
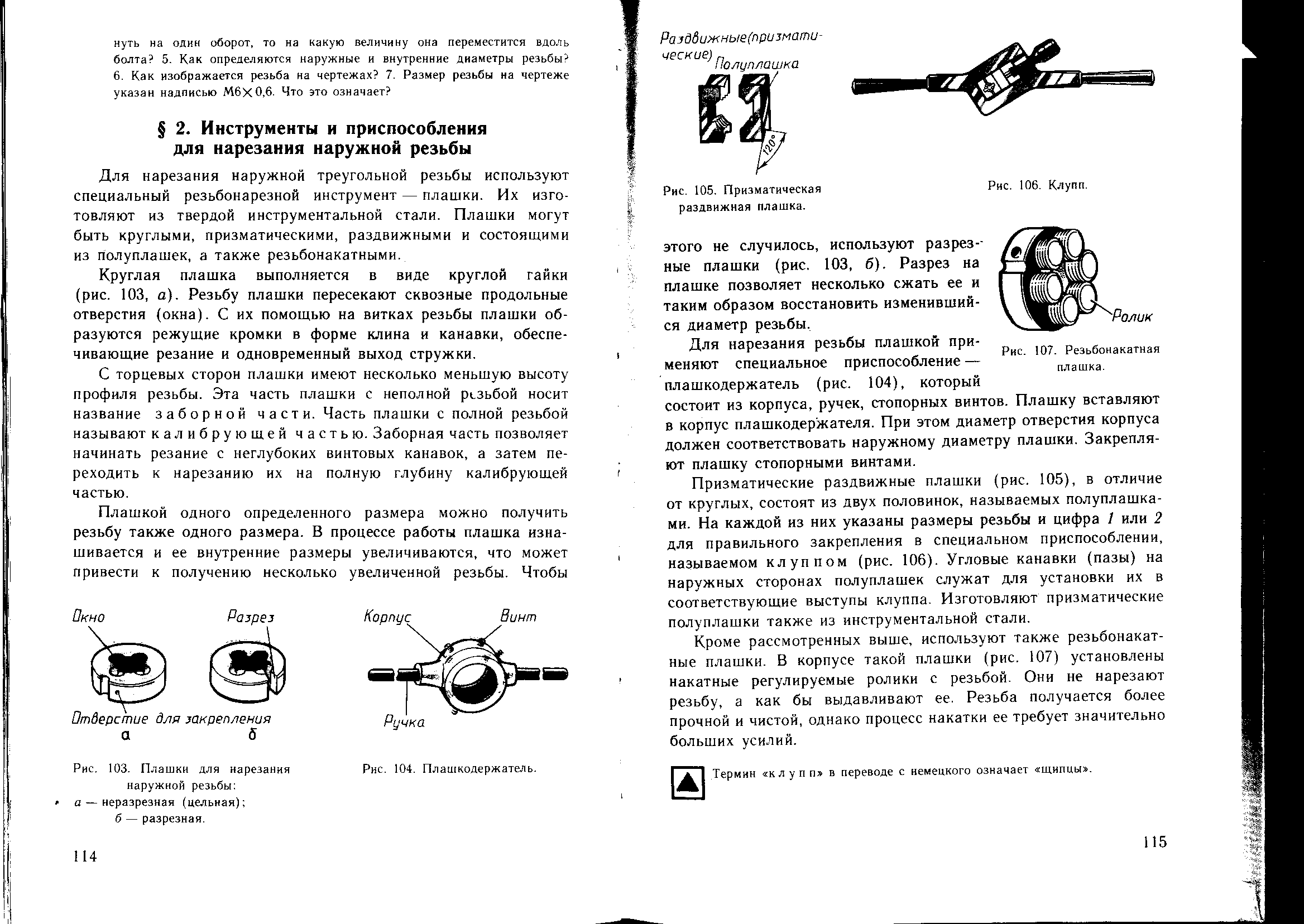
1.2. Разрезные плашки имеют прорезь позволяющую регулировать диаметр резьбы в пределах 0,1 – 0,25 мм, что позволяет регулировать точность нарезания резьбы при износе плашки.
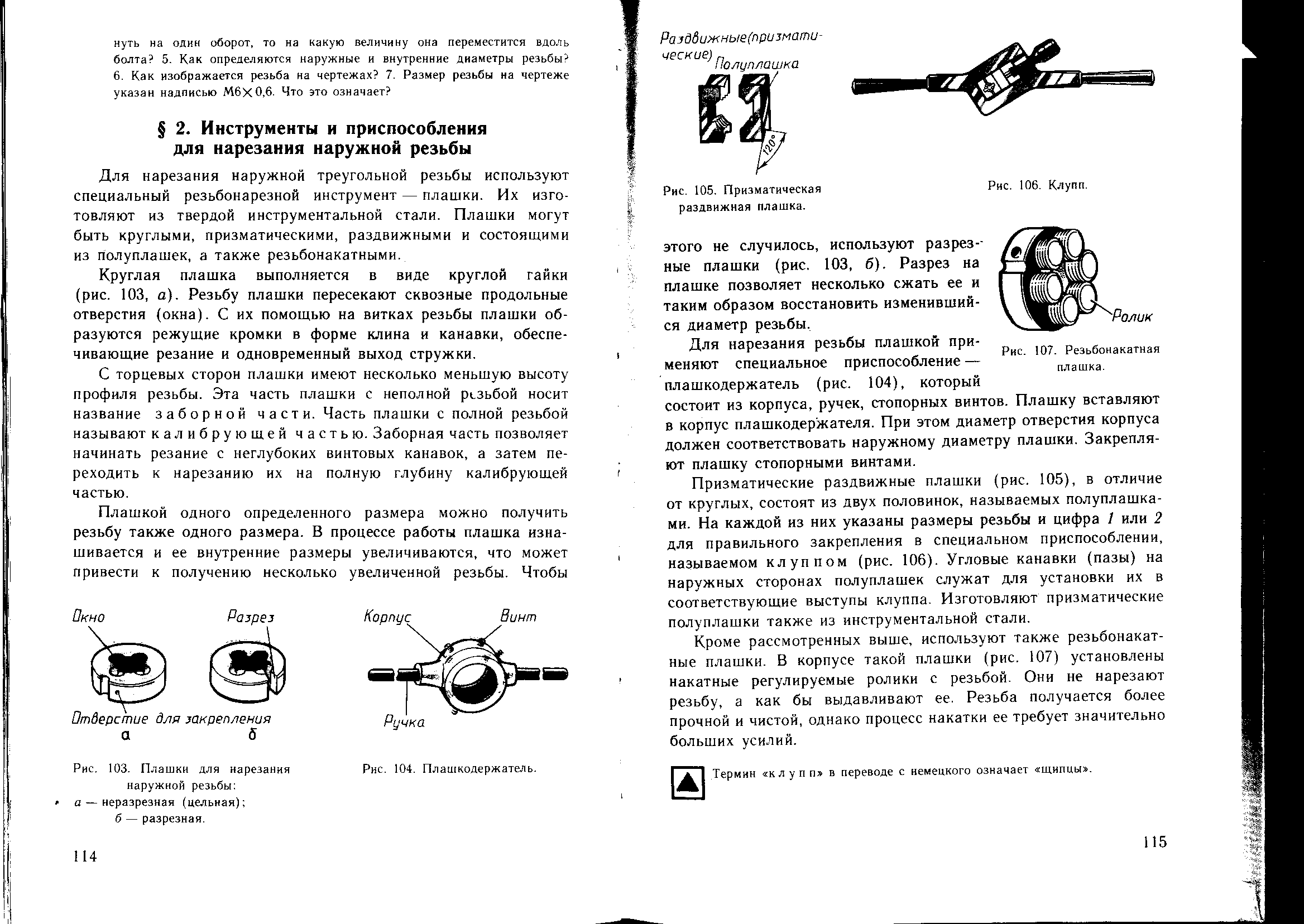
2. Резьбонакатные плашки – в корпусе такой плашки установлены накатные регулируемые ролики с резьбой. Применяется для накатывания точных резьб.
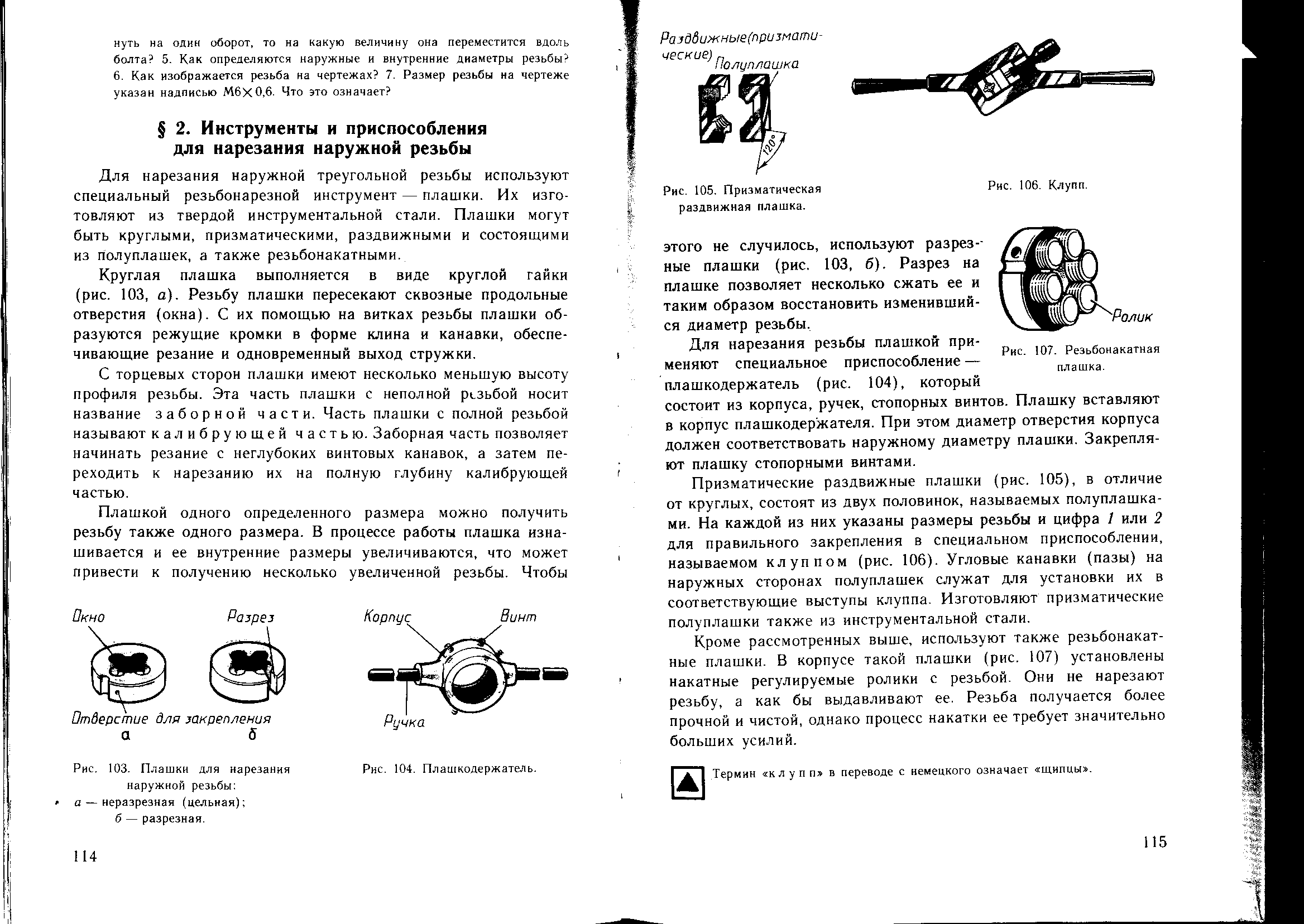
3. Раздвижные призматические плашки (клупп) – состоят из двух половинок на которые нанесены цифры для правильной установки в специальном плашкодержателе.
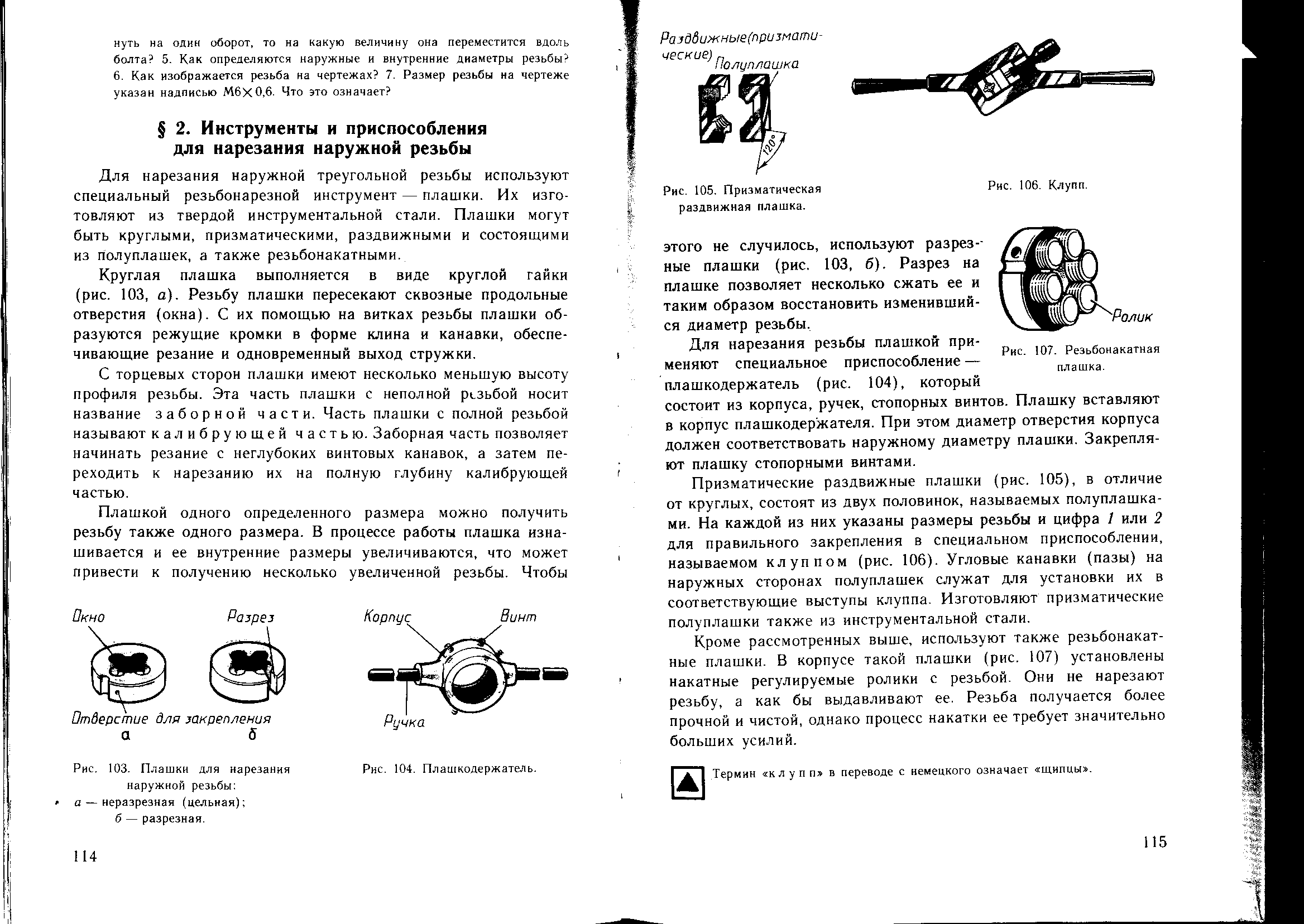
Порядок нарезания наружной резьбы:
1. Подобрать стержень необходимого диаметра для нарезаемой резьбы по специальной таблице.
2. Закрепить плашку в плашкодержателе, зажав ее винтами.
3. Вертикально закрепить стержень в тисках так, чтобы выступающая часть стержня была на 20-25 мм больше длины нарезаемой части.
4. Напильником снять фаску на конце нарезаемой заготовки.
5. Смазать стержень машинным маслом.
6. Горизонтально установить плашку на стержень и нажимая на плашкодержатель вращать его до полного врезания плашки в металл.
7. Далее вращают плашкодержатель на один-два оборота по часовой стрелке и пол-оборота против часовой стрелки для удаления стружки.
8. Обратным вращением снять плашкодержатель.
9. проверить качество резьбы гайкой или калибром.
При нарезании резьбы плашкой надо иметь в виду, что в процессе образования профиля резьбы металл изделия, особенно сталь, медь и др., "тянется", диаметр стержня увеличивается. Вследствие этого усиливается давление на поверхность плашки, что приводит к ее нагреву и прилипанию частиц металла, поэтому резьба получается рваной.
Хорошее качество резьбы можно получить в том случае, если диаметр стержня меньше наружного диаметра нарезаемой резьбы.
Если диаметр стержня будет значительно меньше требуемого, то резьба получится неполной; если же диаметр стержня будет больше, то плашка или не сможет быть навинчена на стержень и конец стержня будет испорчен, или во время нарезания зубья плашки вследствие перегрузки могут сломаться. Практическая работа: организация рабочего места, определение диаметра стержня и выбор плашки. Нарезание наружной резьбы. Контроль качества.
Тема: Нарезание внутренней резьбы.
Цель урока: рассказать о приемах нарезания внутренней резьбы и инструменте, используемом для этого, о мерах предупреждения брака.
Оборудование: заготовки, сверла, сверлильный станок, метчики, таблицы.
Содержание:
Нарезанием резьбы называется её образование снятием стружки (а также пластическим деформированием) на наружных или внутренних поверхностях заготовок деталей.
Инструмент для нарезания внутренней резьбы – метчик.
Метчики бывают: ручные и машинные; для метрической, трубной и дюймовой резьбы; цельные и сборные.
Метчик состоит из рабочей и хвостовой частей.
Рабочая часть представляет собой винт с несколькими продольными канавками и служит для нарезания резьбы.
Рабочая часть метчика состоит из заборной и калибрующей частей.
Заборная часть делается в виде конуса и производит основную работу при нарезании резьбы.
Калибрующая часть направляет метчик в отверстие и калибрует нарезаемое отверстие.
Хвостовик – стержень служит для закрепления метчика в воротке или патроне станка.
Канавки между режущими зубьями нужны для удаления стружки.
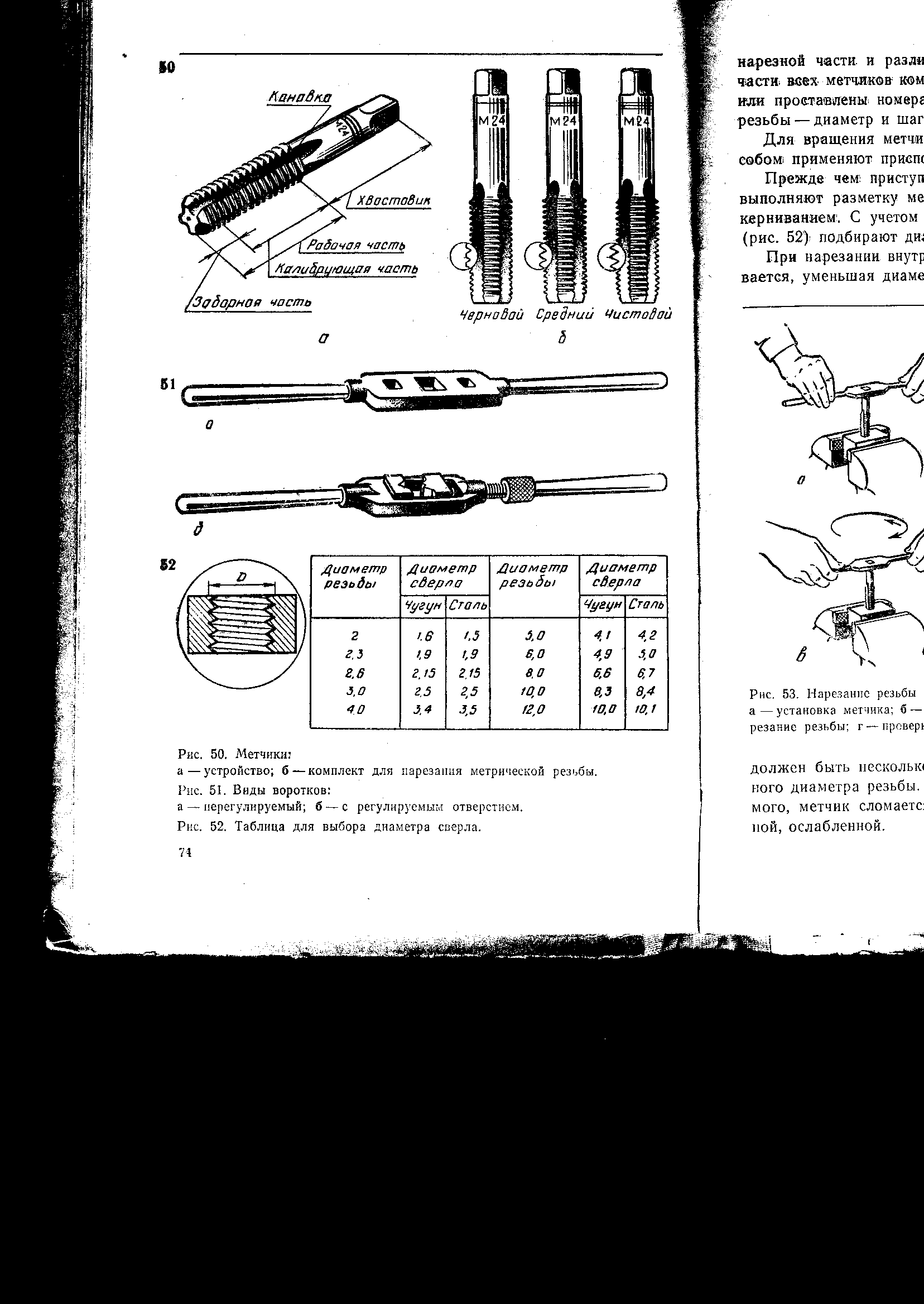
Метчики изготавливают комплектами, состоящими из:
1. чернового метчика;
2. чистового метчика.
Комплекты метчиков могут состоять из трех штук:
1. чернового метчика;
2. получистового метчика;
3. чистового метчика.
Черновой метчик выполняет основную работу и срезает до 60% слоя металла, подлежащего снятию.
Получистовой метчик срезает до 30% слоя металла.
Чистовой метчик придает резьбе окончательную форму и размеры и срезает остальные 10% слоя металла.
Внешне метчики одного комплекта отличаются размерами режущих частей. У чернового метчика она самая большая, получистового – меньше, у чистового – еще меньше.
В комплектах метчики маркируются следующим образом: у чернового на хвостовике одна риска, у получистового – две, у чистового – три.
При нарезании резьбы, метчики закрепляются в воротки различной конструкции.
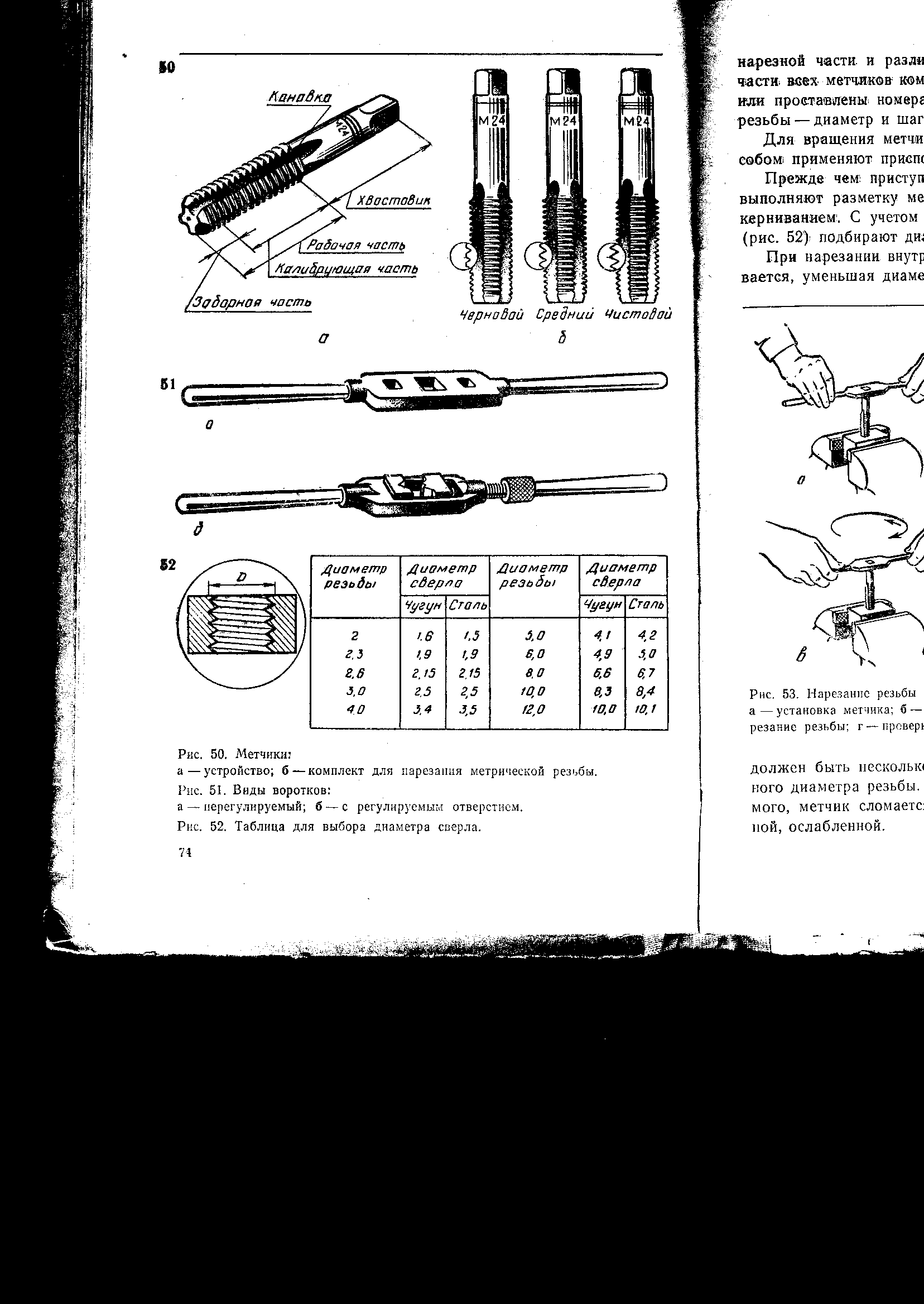
При нарезании резьбы материал частично выдавливается, поэтому диаметр сверла должен быть больше, чем внутренний диаметр резьбы.
Размеры диаметров сверл определяют по специальным таблицам.
Порядок нарезания внутренней резьбы:
1. Определить по справочной таблице диаметр резьбы.
2. Просверлить необходимое отверстие под резьбу.
3. Закрепить заготовку в тиски.
4. В отверстие заготовки вертикально вставить Черновой метчик, проверив по угольнику.
5. Левой рукой прижать вороток к метчику, правой провернуть его вправо, пока метчик не врежется на несколько ниток в металл и не займет устойчивое положение, после чего вороток берут двумя руками и вращают его.
Для облегчения работы вороток с метчиком вращают один-два оборота вправо и пол-оборота влево. Благодаря этому стружка ломается, процесс резания облегчается, резьба получается качественной.
При нарезании резьб используют СОЖ.
6. Закончив нарезание, метчик вывертывают в обратную сторону.
7. Установить в отверстие чистовой метчик, ввернув его без воротка и только после того, как метчик пойдет по резьбе, надевают вороток.
8. Проверить качество резьбы калибром или винтом. Практическая работа: организация рабочего места. Определение диаметра сверла. Нарезание внутренней резьбы.
Тема: Выполнение основных слесарных операций.
Цель урока: выявление и совершенствование учащимися основных приемов ручной обработки металлов при изготовлении изделий.
Оборудование: слесарный верстак, набор слесарных инструментов, измерительный инструмент, заготовки различных изделий, чертежные принадлежности, чертежи, технологические карты.
Содержание:
Опрос учащихся об основных понятиях, инструменте и правилах выполнения:
разметки
рубки,
сборки изделий
клепки
Практическая часть:
Выполнение учащимися чертежей и технологических карт на изготавливаемое изделие.
Выбор заготовок.
Разметка заготовок.
Изготовление и отделка изделия.
Контроль качества.
Оценка качества выполненной работы, подведение итогов усвоения учащимися приемов обработки материалов.
Тема: Устройство настольного горизонтально-фрезерного станка.
Цель: ознакомить с устройством и назначением основных узлов горизонтально-фрезерного станка НГФ - 110Ш. Изучить основные меры безопасности при работе на станке. Научить закреплять заготовку и устанавливать частоту вращения шпинделя.
Оборудование: настольный горизонтально-фрезерный станок НГФ-НОШ.
Содержание:
Фрезерование - это операция механической обработки резанием, при которой многорезцовый инструмент фреза совершает вращательное движение, а обрабатываемая заготовка – поступательное движение.
При фрезеровании получают плоские или фасонные поверхности, пазы, канавки. Изготавливают зубчатые колеса и др.
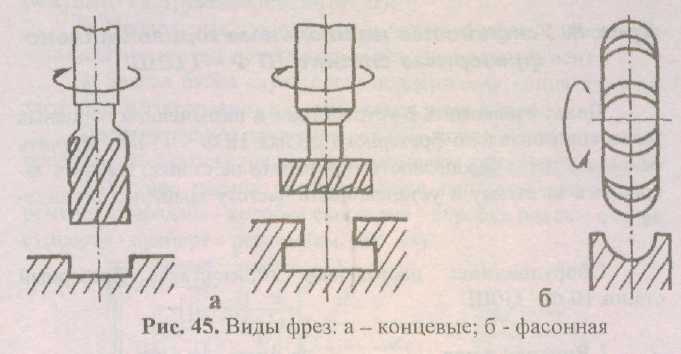
Заготовку устанавливают в тисках или на столе станка.
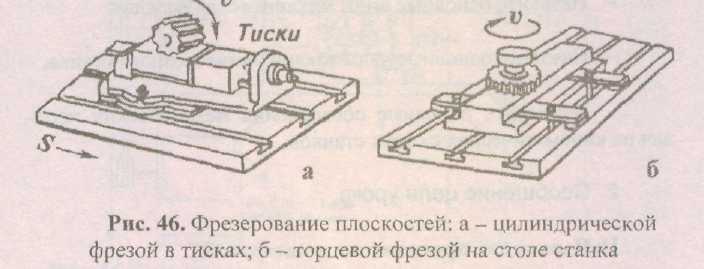
Устройство станка:
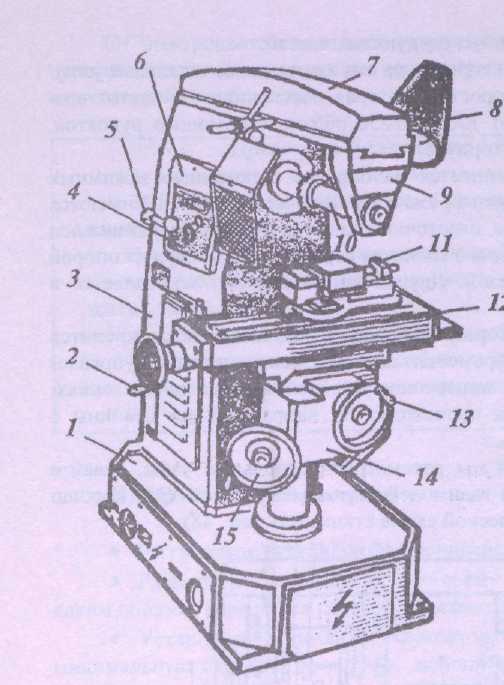
- основание;
– маховик продольной подачи;
3 - корпус станка;
4, 5 - рукоятки переключения частот шпинделя;
6 - коробка скоростей;
7 - хобот;
8 - светильник;
9 - серьга;
- оправка с фрезой;
- тиски; 12-стол;
13 – маховик поперечной подачи;
14 - консоль;
15 - маховик вертикальной подачи.
Этот станок позволяет фрезеровать горизонтальные и вертикальные плоскости, пазы, канавки и т.д. цилиндрическими, торцевыми, дисковыми, коническими, угловыми и фасонными фрезами. Наибольший диаметр фрезы не должен превышать 110 мм.
Теперь, когда мы выяснили возможности станка, давайте рассмотрим отдельные узлы, их назначение и взаимодействие между собой.
Станок состоит из следующих частей:
1.Основание и корпус - на них крепятся все остальные узлы.
2. Коробка скоростей, которая обеспечивает 6 частот вращения шпинделя от 125 до 1250 об/мин с помощью рукояток, расположенных на корпусе.
3.Фреза закрепляется на оправке с помощью зажимных втулок. Для установки фрезы в верхней части корпуса 3 имеются направляющие типа «ласточкин хвост», в которых установлен хобот, к концу которого крепится серьга, которая служит опорой для оправки с фрезой. Другой конец оправки закрепляется в шпинделе станка.
4.Стол, на котором непосредственно или в тисках крепится заготовка, может перемещаться с помощью штурвалов управления в продольном, поперечном и вертикальном направлениях. Перемещение стола происходит по направляющим станины с помощью маховика.
Теперь, когда мы рассмотрели отдельные узлы, давайте посмотрим, как они взаимодействуют межу собой. Это хорошо видно на кинематической схеме станка.
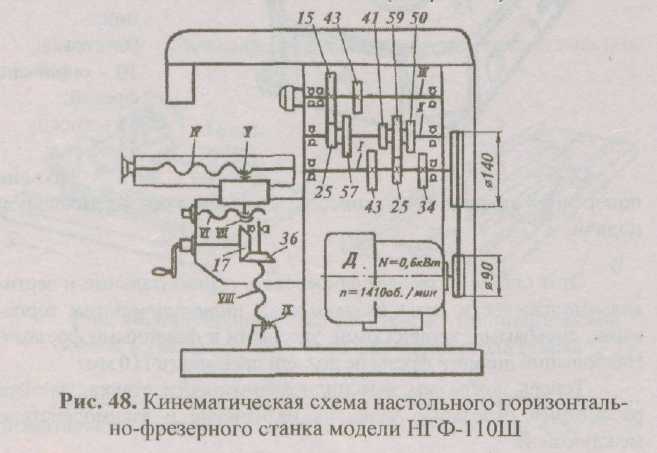
От электродвигателя станка через клиноременную передачу главное движение передается через систему шестерен коробки скоростей на шпиндель.
Правила безопасности:
Не включать станок без разрешения учителя.
Работать на станке только в специальной одежде и защитных очках.
Нельзя трогать руками вращающийся шпиндель.
Рукоятки управления, маховики подач надо вращать плавно, без рывков.
Стол станка не следует перемещать до упора.
Нельзя отходить от включенного станка.
Следует надежно и прочно закреплять заготовку.
Практическая работа:
Рассмотрите несколько фрез и определите их назначение,
Рассмотрите кинематическую схему станка и покажите, каким образом передается главное движение шпинделю.
Установите с помощью рукояток коробки скоростей минимальную скорость вращения, включите и выключите станок. То же проделайте, установив максимальную скорость вращения.
Отсоедините серьгу от хобота, положите на стол. Закрепите на оправку фрезу, поставьте зажимные втулки. Установите на место и закрепите серьгу.
Закрепите тиски на середине стола и установите в них размеченную заготовку. Переместите консоль станка вверх до легкого касания фрезы. Отведите заготовку от фрезы.
• Установите нужное число оборотов фрезы и включите станок. Выполните пробное фрезерование. Выключите станок.
Далее некоторым учащимся предлагается выполнить пробное фрезерование.
Тема: Технология, фрезерных работ по металлу
Цель: изучить устройство и разновидности фрез. Научить выполнению различных видов обработки металла на фрезерных станках.
Оборудование и инструменты: горизонтально-фрезерный станок, наборы фрез и приспособлений для крепления заготовки.
Содержание:
Фрезерование осуществляется вращающимся режущим инструментом, называемым фрезой. При обработке фрезами образуется прерывистая стружка переменного сечения.
> Сравнить со стружкой, образующейся при обработке резцом. Она непрерывная, постоянного сечения.
Зубья фрезы могут располагаться как на цилиндрической поверхности, так и на торце.
Фрезы, как правило, многозубый инструмент.
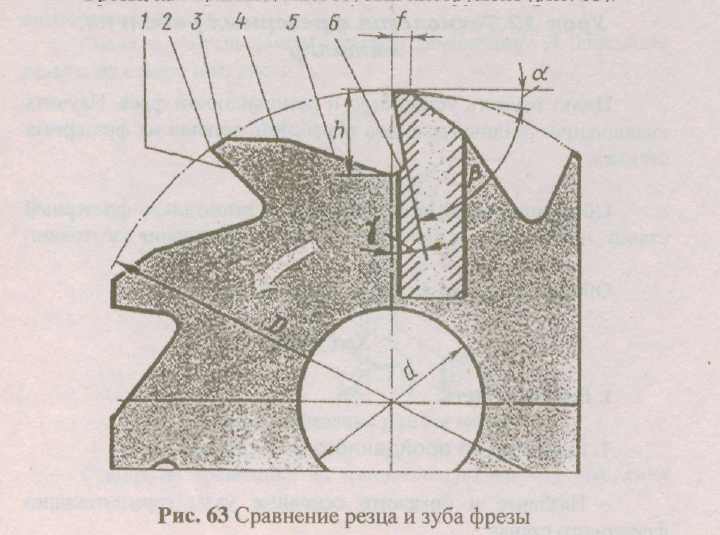 Каждый зуб фрезы представляет собой простейший инструмент - резец.
При фрезеровании плоскостей торцовыми и цилиндрическими фрезами различают:
|
|
|